Wireless Vibration Sensors in Mining: Enhancing Safety, Efficiency and Maximising Production
- Miniotec - Intelligent Solutions
- May 15, 2023
- 23 min read
Updated: Feb 28
How Wireless Vibration Sensors Drive Operational Efficiency and Improve Condition Monitoring in the Mining Industry
Within the article we will consider:
The role of digital innovation, specifically IIoT and Wireless Vibration Sensors, in addressing mining industry challenges such as workforce shortages and ESG practices.
The integral function of Wireless Vibration Sensors in data acquisition, asset performance monitoring, and facilitating the digital transformation within the mining sector.
The multifaceted benefits of these sensors in improving predictive maintenance strategies, offering enhanced analytics and enabling real-time monitoring in hard-to-reach mining locations and widely dispersed mining operations.
Introduction
In the high-risk environment of the mining industry, where safety is a priority, digital innovation and ground-breaking approaches in asset management are paving the way towards safer, more efficient operations. The mining sector, particularly within the Australian market, is currently faced with workforce shortages, therefore maintaining machine health status and maximum output capacities requires the adoption of automation technologies such as the Industrial Internet of Things (IIoT) and Industrial Vibration Sensors to mitigate operational risks. Meanwhile, a drive for Environmental, Sustainability and Governance (ESG) practices is also encouraging the industry to innovate and promote sustainability in mineral extraction activities.
Enter IIoT technology, a key player in the Industry 4.0 sector (Fourth Industrial Revolution). Within the IIoT scope, industrial Wireless Vibration Sensors stand as a transformative solution in the mining sector, helping to deliver Digital Mining. These intelligent sensors have emerged as an integral component in the predictive maintenance market, serving as the backbone for a robust condition monitoring process.
Elevate your asset management and optimise your operations: take our online IIoT opportunity evaluation today for actionable insights.
Wireless Vibration Sensors in mining help create an accurate and reliable data acquisition system through wireless connectivity. Their ability to deliver vibration analysis and provide precise measurements of various critical parameters such as Acoustic Emissions, RPM, Magnetic Flux, Temperature sensor and Humidity, enables comprehensive asset performance monitoring, thereby contributing to the improvement of asset reliability engineering and operational effectiveness.
These remote vibration sensors, designed specifically for industrial environments, including underground mines, are not just tools for monitoring equipment vibrations. They are the driving force behind a mining operation's digital transformation journey, ensuring long-term reliability of critical machinery and enhancing operational efficiency through data-driven decisions.
As we delve into the world of Wireless Vibration Sensors, we will explore how this wireless IIoT technology is enhancing safety, working efficiency, operational performance and maximising production in the mining industry. From the simple sensor installation steps to the enhanced analytics options they offer, we will discuss how these sensors simplify asset monitoring and enable real-time vibration monitoring in difficult-to-access spots in all mining conditions.
We will also highlight the role of wireless sensors in predictive maintenance strategies, providing immediate response and enabling condition-based data to inform maintenance action, effectively reducing equipment downtime. The integration of these sensors with the latest AI and machine learning capabilities can lead to anticipatory upkeep, moving from reactive to proactive maintenance planning.
Stay with us as we navigate the evolving landscape of wireless vibration monitoring and how this core innovation hub is revolutionising mining operations. Let us embark on this journey of digital automation in the resource industry, where wireless monitoring and sensor technology are transforming traditional practices into modern, sustainable operations.
I. The Pivotal Role of Equipment Health in Mining
A.) Why Wireless Vibration Sensors are Important for Equipment Health and Reliability, Maintaining Safety and Productivity

In the mining sector, asset performance is
integral for maintaining safety and productivity. Ensuring the operational health of mining machinery and components is crucial, particularly in underground mining where high-risk environments demand optimal performance of machines.
Implementing health monitoring devices, like wireless triaxial vibration sensors, enables access to real-time monitoring data, leading to anticipatory upkeep and promoting a safer working environment whilst improving plant efficiency. These intelligent sensors make it possible to deliver a predictive maintenance program that detects equipment vibrations that deviate from the normal range, providing early equipment failure indications, critical for proactive maintenance plans and fault identification.
B.) The Real Costs Associated with Equipment Downtime and Maintenance
Unanticipated downtime is a significant cost driver in the mining industry. Critical assets such as conveyors and conveyor components, crushers, motors, pumps, gearboxes and other rotating mining machinery are essential for extracting valuable metals and minerals and any disruption can lead to significant economic value loss. The costs are not just limited to repair or bearing replacement; there is also the loss of production during downtime, which can affect overall profitability. A wireless remote machine condition monitoring system offers a solution by identifying early signs of machine breakdowns, enabling timely maintenance action, thereby reducing asset downtime and enhancing operational efficiency.
For more information on the impact of deferring maintenance, have a read of this article: "The True Cost of Deferred Maintenance".
C.) The Hidden Costs of Inefficient Maintenance Strategies
Traditional maintenance strategies, often relying on hand-operated data gathering, can be both time-consuming and prone to errors. Moreover, they do not provide the consistent observation needed to ensure maximum machine operational time. Inefficient maintenance strategies can lead to a cyclical pattern of equipment failure and repair, escalating maintenance costs and curtailing machine fitness. Wireless condition monitoring, especially within a remote vibration detection system, can break this cycle by providing precise and dependable information, enabling predictive maintenance and ultimately leading to asset reliability improvement.
By leveraging the power of IIoT wireless technology and remote vibration sensors, mining operations can transform their maintenance strategies, reduce downtime and optimise the performance of their assets. These advancements in digital automation are a crucial step in driving innovation in the industry's journey towards increased safety, efficiency and productivity.
In the next section, we will delve deeper into asset health monitoring sensor specifications of wireless technology and its advantages over traditional wired sensors.
II. Wireless Vibration Sensors: Harnessing the Power of Proactive Maintenance in Mining Operations
A.) A Detailed Overview of Wireless Vibration Sensor Technology
Wireless Vibration Sensors, a ground-breaking approach in the realm of industrial condition tracking, have become indispensable, particularly within the mining sector. These innovative devices, replete with advanced features such as accelerometers and RMS data analysis, are meticulously designed to monitor the vibration levels of machinery and components. They provide precise measurements of critical parameters and are the cornerstone of real-time true asset predictive maintenance, a form of anticipatory upkeep. Leveraging the power of advanced IoT technology, these sensors transmit data wirelessly, facilitating remote machine monitoring even in the most inaccessible areas within a mining operation, such as atop cooling towers or within the depths of an underground mine.
B.) Advantages of Wireless Vibration Sensors Over Traditional Wired Sensors
1.) Ease of Installation

One of the most significant advantages of wireless sensor technology over traditional wired systems is the ease of sensor installation. The installation steps for wired systems necessitate considerable infrastructure, encompassing trenching, cabling and setting up installation points, which can be both costly and labour-intensive. Conversely, wireless sensor setup is straightforward and can be carried out by the existing workforce, causing minimal disruption to the mining operation. Installation and maintenance costs are significantly lower using wireless vibration solutions compared to traditional fixed wired solutions.
2.) Scalability
Wireless sensor systems offer superior scalability over their wired counterparts. As the mining operation expands or as monitoring needs evolve, additional wireless sensors can be smoothly integrated into the existing wireless monitoring system. This adaptability makes wireless sensors within a comprehensive wireless solution an attractive option for large-scale, challenging mining environments to improve machine uptime.
3.) Reduced Maintenance Requirements
Wireless sensors, such as the solution offered by Miniotec, come with a user-replaceable battery boasting long battery life due to low power consumption. This capability significantly reduces sensor replacement costs associated with sensors lacking interchangeable batteries. The wireless data collector obviates the need for any cable or connector replacements, making the system robust, rugged and reliable.
C.) Key Features of Wireless Vibration Sensors Suited for Mining Applications
1.) Rugged Design and Durability
The harsh mining conditions necessitate sensors that can operate reliably even in extreme, potentially hazardous environments. With their rugged design, high G range and robustness, along with an IP68 specification dust and water resistance rating, the best wireless vibration sensors can withstand the rigors of mining environments.
2.) Seamless Connectivity
Wireless Vibration Sensors provide seamless wireless connectivity, transmitting real-time operational data to a digital platform or other IIoT systems. This live vibration tracking enables an immediate response to potential problems, thereby optimising performance and increasing the efficiency of tasks.
3.) Flexibility and Expandability
Wireless sensor systems exhibit flexibility and scalability, aligning with the dynamic needs of mining operations. As the data requirement increases, additional sensors can be easily added or swapped out, offering enhanced analytics features.
4.) Real-Time Data Transmission
Wireless vibration technology offers quick feedback, transmitting vibration and surface temperature integrated sensor data in real-time. This capability enables remote vibration detection and specific fault identification for precise and dependable industrial condition monitoring and failure detection.
5.) Interoperability with Existing Systems
Wireless Mining vibration sensors can connect to existing historians through compatible protocols such as REST-API or MQTT, allowing for the aggregation of data centrally within existing platforms. This feature enables the analysis and visualisation of sensor data for actionable insights, thereby promoting innovation in the mining industry.
In the next section, we will delve into the practical applications of these wireless vibration sensors in mining, highlighting how they can play a pivotal role in early problem detection and prevention, thereby leading to improved asset performance and management.
III. Practical Applications of Wireless Vibration Sensors in Mining Operations: Enhancing Operational Efficiency and Safety
A.) Detailed Use Cases: Monitoring Conveyor Belts, Crushers, Heavy Machinery and Mining Infrastructure for Enhanced Performance Information
Wireless vibration sensors, as part of modern vibration detection technology, have an extensive scope of application in the mining sector. They play a pivotal role in the continuous monitoring of conveyor belt pulleys and associated componentry, a critical asset in the mineral extraction process. Real-time vibration measurements help in the early detection of any potential issues, thus mitigating the risk of unexpected shutdown and increasing equipment operational time.
In addition to conveyor belts, these wireless sensors, within a condition monitoring solution, are instrumental in overseeing the health of crushers, compressors, generators, electric motors and other heavy machinery. For instance, vibrating screens, essential in mining activities for separating materials based on size, can be effectively monitored for bearing defects or compromised ball bearings, preventing further damage and enhancing the machine's fitness.
Moreover, these sensors are also deployed for the health tracking of critical mining infrastructure such as ventilation fans in underground mines. By accurately measuring vibration levels, these sensors can spot early signs of malfunction or failure, thereby ensuring a safe and healthy environment, making safety priority in these high-risk environments.
B.) The Role of Wireless Sensors in Early Problem Detection and Prevention: Anticipatory Upkeep for Mining Equipment
Wireless monitoring technology is at the heart of early problem detection and prevention, forming a cornerstone of the digital innovation in mining operations. They offer continuous monitoring of the operational health and performance of machines, identifying deviations from normal ranges or cyclical patterns indicative of potential issues. This constant observation helps in predicting the remaining useful life of individual components, paving the way for a proactive maintenance plan.
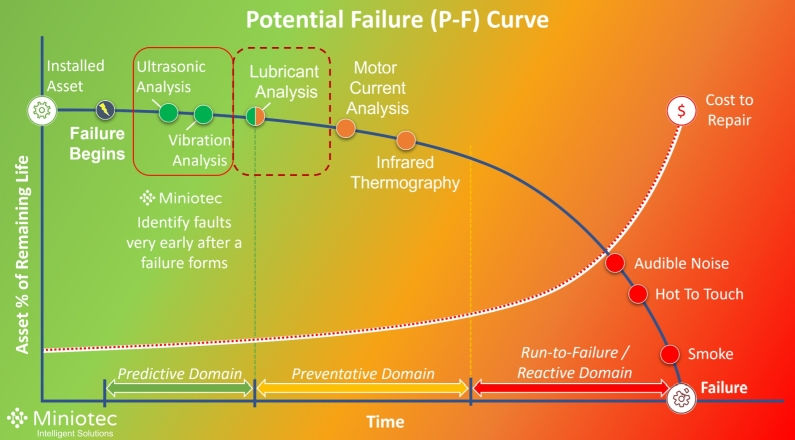
With the integration of predictive analysis and data analytics in line with the industry-standard P-F curve, these sensors enable early identification of developing faults in industrial assets. This early fault identification coupled with timely maintenance intervention reduces the risk of catastrophic failures and their associated costs, thereby promoting the reliability enhancement of mining operations.
C.) The Importance of Continuous Monitoring in Mining Operations: Promoting Operational Productivity and Safety
The mining industry, being a hazardous environment, prioritises the health and safety of workers. In this context, continuous monitoring of machinery and infrastructure using wireless vibration sensors becomes crucial. These sensors provide immediate response regarding machine health status, helping identify potential risks before they escalate into severe issues.
Furthermore, the analysis of operational data from continuous machine health monitoring empowers mining professionals to optimise the efficiency of tasks, thus contributing to the overall operational productivity. This form of data-driven decision-making forms an essential part of the digital transformation journey of mining operations.
In the subsequent section, we delve into the transformative potential of implementing wireless vibration sensors in mining operations, encompassing improved safety, reduced equipment downtime and enriched decision-making driven by real-time data insights.
IV. Transforming Mining Operations: The Benefits of Implementing Wireless Vibration Sensors
A.) Improved Safety Through Early Detection of Potential Equipment Failures
The application of wireless vibration sensors as a reliability enhancement solution represents a ground-breaking approach towards bolstering safety within mining operations. Live vibration tracking enables early detection of machine failure symptoms, such as compromised ball bearings, critical gearbox issues, or unusual conditions in rotating mining machinery. This instant feedback and alert progression in potential problems allow for anticipatory upkeep measures to be taken before a minor issue escalates into a major catastrophe, thereby drastically improving safety across the entire mining operation, especially in hazardous locations at height or environments like underground mines.
Here is an interesting article on asset criticality and IIoT: "Which Equipment is Most Suited for IIoT Monitoring and Maintenance?"
B.) Reduced Downtime and Maintenance Costs
Unexpected shutdowns are a significant expense factor in the mining industry, both in terms of lost mineral extraction and the costs associated with emergency maintenance or repair intervention. Wireless vibration sensors deliver consistent observation and provide precise and dependable information about the Machine Health Status, enabling a transition from reactive maintenance to a prognostic maintenance strategy. This approach reduces equipment downtime by scheduling Maintenance Actions when they are truly needed, letting your ‘dumb’ machines talk, based on the condition of the equipment rather than a predetermined schedule, leading to substantial cost savings.
C.) Optimised Equipment Performance and Lifespan
Wireless sensors not only assist in fault identification but also contribute to performance optimisation. They offer precise measurements of critical parameters such as acoustic emissions, turning frequencies, magnetic flux, temperature data and humidity, thereby enabling maintenance and reliability professionals to make data-driven decisions to improve machine longevity and maximise capacity. With the ability to monitor vibration energy levels and other key components, these sensors ensure that machinery operates reliably and within their normal range, extending the equipment's operational time.
D.) Enhanced Decision-Making with Real-Time Data Insights
Wireless vibration sensors contribute to the digital automation journey of mining operations by providing real-time operational analytics for enhanced analytics features. This data, combined with artificial intelligence and prescriptive analytics, can offer invaluable insights about the performance effectiveness, the quality of tasks and overall plant effectiveness. In this way, wireless sensor technology facilitates data-driven decisions, leading to performance monitoring and improved overall productivity.
E.) Increasing Overall Productivity and Profitability
By promoting safety, reducing downtime, prolonging the lifespan of machinery, reallocating routine and mundane activities (i.e., hand-operated data gathering) to value-adding tasks and enhancing decision-making capabilities, wireless vibration sensors significantly increase overall productivity and profitability in mining operations. By simplifying asset monitoring with sensor implementation and delivering timely and accurate data, these sensors empower mining professionals to focus on core operations and strategic planning, leading to tangible economic value for the mining sector.
In the next section, we will explore the integration of wireless vibration sensors with IIoT wireless technology, which can further amplify these benefits and unlock new opportunities for the mining sector.
Read how IIoT supports Digital Twins in Transforming The Energy Sector: "IIoT and Digital Twin Technology: Transforming Energy and Industrial Operations"
V. Harnessing the Power of IIoT: Integration of Wireless Vibration Monitoring with IIoT Systems to Deliver a Predictive Maintenance Solutions
A.) Connecting Wireless Vibration Sensors to Existing Asset Management Historians
The integration of wireless vibration sensors into Industrial Internet of Things (IIoT) systems marks a significant milestone in the digital transformation journey of the mining industry. A pivotal aspect of this integration process involves connecting these smart sensors to existing Historians - databases that document and recall time-based information. By capitalising on the wireless data acquisition capabilities of these sensors, mining operations can effectively capture, aggregate and store all types of integrated sensor data, as well as other condition-based data such as RPM and magnetic flux, directly into their existing infrastructure. These wireless monitoring solutions with seamless connectivity and data acquisition systems bolster the capacity for remote machine monitoring, thereby streamlining asset management.
B.) Analysing and Visualising Sensor Data for Actionable Insights
A standout advantage of IIoT technology lies in its robust capacity for data analytics and visualisation. Wireless vibration sensors provide accurate and reliable data that can be processed by advanced IIoT systems to deliver anticipatory upkeep strategies. By deploying machine learning and AI-powered predictive maintenance systems, these systems can analyse sensor data to identify patterns, forecast equipment downtime and visualise asset health. This approach offers immediate response and actionable insights to reliability experts, fostering innovation and enhancing overall operational effectiveness of mining operations.
C.) Implementing Predictive Maintenance Strategies with the Help of Machine Learning and AI
Wireless IIoT solutions are instrumental in providing the necessary data for implementing predictive maintenance strategies. Machine learning algorithms can learn from the patterns and trends in the sensor data to predict potential equipment failures and provide timely alert progression. The integration of remote sensor technology and machine learning enables a shift from reactive maintenance to predictive and even prescriptive analytics, resulting in improved asset reliability improvement and significant reductions in maintenance intervention costs.
By harnessing the power of IIoT and embracing this ground-breaking approach, mining operations can not only improve their asset performance management but also take proactive steps towards sustaining their valuable metals and minerals extraction processes. This digital innovation is already revolutionising mining sectors globally.
In the following section, we will delve into the potential challenges that may arise when implementing this wireless sensor technology and discuss strategies to effectively address these obstacles.
VI. Overcoming Challenges in the Implementation of Wireless IIoT and Real-Time Monitoring
A.) Addressing Potential Issues and Challenges in Adopting Wireless Vibration Sensors
While the adoption of wireless vibration sensors offers immense benefits for mining operations, it is not without potential challenges. Some of the key hurdles are the installation process and staff training, largely due to a staff shortages or staff turnover. However, it is essential to view these activities as an anticipatory upkeep, an investment towards long-term reliability and efficiency monitoring, as they can significantly reduce the costs associated with asset downtime and hand-operated data gathering.
Another potential challenge lies in ensuring that wireless sensor technology can withstand the harsh mining environments, including underground mines. Recognising their rugged design, durability and IP68 ingress protection rating indicating dust and water resistance, wireless vibration sensors such as those delivered by Miniotec are designed to operate reliably even in high-risk environments.
B.) Strategies for Successful Implementation and Employee Training
Successful implementation of a wireless vibration sensor system involves a strategic approach that considers the unique needs of the mining operation. It is crucial to select sensors with the appropriate specifications, including maximum communication range in industrial environments, battery life and low energy usage. This promotes a proactive maintenance plan which focuses on machine health status, fault identification and asset performance.
For more information on considerations for choosing a Wireless Monitoring solution that includes temperature and vibration measurements and is suitable for remote and hard-to-reach places in a mining site, read this article: "Introduction to Wireless Vibration Monitoring - What a "Best-In-Market" Sensor & Solution Considers".
Implementing a wireless IIoT solution also requires some training of the workforce. Even the most advanced features of a wireless vibration monitoring system are of little value if employees do not understand how to use them effectively. Training programs can help staff understand how to correctly install and maintain their sensors and take the necessary actions based on the data delivered from real-time vibration monitoring.
Moreover, mining professionals should not overlook the importance of adopting reliable Tier 1 wireless vibration solutions for the mining industry, which connect seamlessly, deliver robust, rugged and reliable sensor data and deliver true predictive maintenance advanced analysis options using data analytics and machine learning.
Next, we will explore some success stories of wireless vibration sensors in mining operations, highlighting the transformative impact of this innovative approach in the real world. This will include exploration of how maintenance prediction, machine condition monitoring and data-driven decisions can lead to operational efficiency and performance optimisation in the mining sector.
VII. Success Stories: Wireless Monitoring Solutions in Mining Operations
A.) Case Study 1: A Mining Company that Successfully Reduced Downtime with Wireless Vibration Sensors
One of the major players in the Australian mining sector had been grappling with asset downtime, particularly in their critical asset - a conveyor belt system. The company relied heavily on manual data collection for condition monitoring, which not only was labour-intensive but also inefficient due to the high-risk environment and staff changes.
After a thorough evaluation, the company decided to transition towards a predictive maintenance strategy and adopted a modern wireless vibration monitoring system. The wireless vibration sensors were installed on key components of the conveyor belt, including the bearing housing of all pulleys and all rotating machinery.
The sensors' robust, rugged and reliable design, along with its IP68 specification and most importantly their ability to individually connect to the local LTE wireless network, made them an ideal choice for the demanding mining environment. Each sensor was installed in less than 5 minutes each and required no Gateways, therefore no trenching, wiring or power, The sensors' advanced features, such as the ability to provide accurate readings of vibration levels, temperature and acoustic emissions, transformed their condition monitoring process.
The real-time monitoring enabled by these sensors and the wireless remote machine condition monitoring system provided instant feedback about the health of the conveyor belt system. Anomaly detection and failure mode analysis became simpler and quicker, allowing for maintenance intervention before a full-fledged system failure could occur.
Within a few weeks, the system detected and alerted the mining company of separate issues relating to ‘unbalance’ and ‘bearing race’ issues which prevented an unplanned downtime event and therefore avoided any production loss thus the system’s return on investment (ROI) was effectively immediate. The mining company saw a significant reduction in downtime, which led to substantial economic value. They also reported improved safety standards and plant efficiency, displaying the transformative potential of wireless vibration sensors in mining operations.

B.) Case Study 2: A Unique Application for IIoT Wireless Vibration Sensors By Monitoring a Non-Rotating Static Chute's Vibration Data for Early Blockage Detection
A significant challenge faced by a mining company was the frequent occurrence of ore build-up on the vibratory feeder pan, which often resulted in contact with the static chute. This issue led to structural cracks and, in extreme cases, catastrophic failures. These failures had severe financial implications, costing hundreds of thousands of dollars in repair and causing over 24 hours of lost production each time.
To tackle this issue, the maintenance team turned to an innovative method of real-time remote monitoring by implementing wireless vibration sensors on eight (8) chutes. The wireless sensor solution, without any need for wires or gateways, was installed in less than five (5) minutes, reporting data shortly after. The sensor's advanced analytics and their unique capability to modify their firmware to better suit the use case, allowed the team to repurpose an efficient solution for monitoring not just rotating equipment, as is typical, but also to detect chute and feeder contact as an early warning sign of potential blockage issues.

Shortly after the sensor installation, two (2) separate chutes, on different dates, sent notifications of increasing velocities (moving averages). This alert prompted the maintenance team to inspect and clean the chutes as required. The team found an ore build-up at the back and sides of the feeders, which led to increased vibration in the chute. Thus, proactive cleaning was carried out, effectively preventing structural failure.
The incorporation of wireless vibration sensors had a transformative impact, generating value across multiple domains:
Safety:
The sensors enabled real-time monitoring of equipment health, reducing the risk of catastrophic failures and thereby enhancing overall workplace safety. Productivity: The sensors' ability to detect early signs of wear and operational changes facilitated a shift towards predictive maintenance, which minimised downtime and ensured efficient equipment operation.
Cost:
Condition monitoring through the sensors curtailed maintenance costs by identifying problems before escalation, preventing expensive repairs and equipment replacements. Given that a previous failure had resulted in over $100k+ in maintenance costs and 24 hours of lost availability, the return on investment (ROI) was almost immediate, with virtually zero installation costs due to the absence of cables or gateways.
Revenue:
Improved equipment reliability and uptime, courtesy of the wireless sensors, directly increased production capacity, thereby boosting revenue growth. Scaling this solution across other company sites would invariably multiply savings exponentially.
Culture:
The implementation of IIoT solutions fostered a proactive maintenance culture within the organisation, encouraging innovation and a forward-thinking mindset.
Social Value:
By enhancing industrial efficiency and reducing unplanned downtime, the wireless vibration sensors contributed to the sustainability of industrial operations, benefitting both the environment and society. The goal was not to replace human workers but to allow the team to focus on more proactive activities that add more value.
Overall, this case study exemplifies how the effective integration of IIoT and wireless vibration sensor technology can revolutionise traditional mining operations, leading to substantial improvements in safety, productivity and cost-efficiency.
For further case study examples, please refer here.
In Summary: The Gateway to Enhanced Machine Health through Wireless Vibration Analysis and IoT Integration
In this era of digital innovation, the future of the mining sector is inextricably tied to the digital transformation journey. As we traverse the path of Industry 4.0, the integration of the Industrial Internet of Things (IIoT) and specifically, the wireless vibration sensors, is no mere innovative method, but a ground-breaking approach that is revolutionising the management of mining operations. Throughout this article, we have explored the transformative potential of wireless vibration sensors in the mining industry, focusing on the advanced features offered by Miniotec. These smart sensors have proven their value across a variety of mining conditions, enhancing the operational effectiveness of numerous mining companies across continents. The benefits of wireless vibration systems for mining operations are proven.
Through real-life case studies, it is evident that wireless vibration sensors significantly contribute to reducing asset downtime, bolstering operational efficiency and, importantly, elevating worker safety. With the capacity to provide immediate response, precise and dependable information and accurate readings of critical parameters such as vibration levels, temperature and acoustic emissions, these sensors empower mining professionals to transition from reactive to anticipatory upkeep, indicative of a shift to predictive maintenance strategies.
But the potential of wireless vibration sensors extends beyond individual machinery and components. By interfacing these sensors with IIoT systems and their own Historians, mining operations can harness the power of predictive analytics, machine learning and Artificial Intelligence (AI). This integration not only enables enhanced analytics for more accurate condition monitoring but also paves the way for prescriptive analytics, where data-driven decisions can inform strategic planning and decision-making processes.
Despite the clear benefits, the path to the adoption of wireless sensor technology is not devoid of challenges. From ensuring seamless wireless connectivity for integration with existing systems, to addressing potential issues like signal interference in industrial environments and arranging for workforce training – these issues need to be navigated meticulously. However, with a robust strategy and a clear vision, these challenges can be successfully overcome. Looking ahead, the role of IIoT in mining operations is set to evolve and expand. The advent of more advanced wireless monitoring solutions and intelligent sensors may lead to further enhancements in mining operations, thereby driving innovation and promoting sustainable practices.
In conclusion, the mining industry stands at the precipice of a technological revolution, with wireless vibration sensors leading the charge. It is an exciting time for mining companies to consider adopting these advanced solutions, not just as a means to improve safety, efficiency and profitability, but to reshape the very landscape of mining operations in the age of digital transformation.
Miniotec is at the forefront of delivering the benefits of IIoT wireless technology and is committed to supporting organisations seeking a step change in the performance of their operations, be it in mining or any other sector. We are eager to share our expertise and digital lessons learnt to ensure success is delivered in the most efficient time and cost possible, thereby optimising the asset performance and overall health of operations.
Frequently Asked Questions
Q: How can we utilise the real-time data insights provided by wireless vibration sensors to improve decision-making processes at the strategic level in our mining operations?
A: Real-time data insights from wireless vibration sensors can significantly enhance strategic decision-making in mining operations. These sensors, forming part of the Industrial Internet of Things (IIoT), provide immediate feedback on various aspects such as vibration levels, acoustic emissions and temperature, all of which are essential parameters in maintaining optimal machinery health.
For instance, observing a cyclical pattern in vibration data from a critical gearbox might indicate a damaged bearing requiring maintenance intervention. This immediate insight allows decision-makers to schedule maintenance promptly, thus preventing further damage, costly repairs, or potential equipment failure.
Moreover, the integration of wireless vibration sensors with machine learning can further enhance predictive maintenance strategies. By analysing and visualising sensor data, algorithms can detect subtle patterns or changes in equipment behaviour, often before a human operator would notice them. Such early detection allows for proactive maintenance, preventing unplanned downtime and potentially extending machine longevity.
Q: Considering the sustainability practices in the mining industry, how can the adoption of wireless vibration sensors contribute to our environmental responsibility?
A: The adoption of wireless vibration sensors contributes to sustainability practices in the mining industry in several ways. First, by enabling more effective condition monitoring and predictive maintenance, these sensors can help minimise the waste associated with premature part replacement and inefficient use of resources. This contributes to a reduction in the mining operation's overall carbon footprint.
Furthermore, the use of wireless vibration sensors can contribute to more efficient use of energy. By continuously monitoring the operational health and performance of machines, these sensors can help identify underperforming equipment that may be consuming more energy than necessary. Through this, necessary adjustments can be made, resulting in energy savings and a reduced environmental impact.
Additionally, the data collected from these sensors can be used to optimise mining processes, leading to reduced energy consumption and lower emissions. A good article that discusses this can be found here: "IIoT and Decarbonisation Projects: Assisting Emission Reductions Across Scopes 1, 2 and 3".
Lastly, the wireless nature of these sensors reduces the need for extensive cabling and associated installation efforts, leading to less disturbance to existing operations during the installation process. This presents a significant advantage.
Q: In terms of asset health monitoring, how can wireless vibration sensors provide us with a more comprehensive understanding of the state of our critical machinery, such as conveyors components, pumps and motors?
A: Wireless vibration sensors significantly enhance asset health monitoring by providing a real-time, comprehensive view of the operational status of critical machinery. These sensors detect changes in vibration levels and temperature, key measurements that indicate machine health. For instance, an increase in vibration energy levels could signify a damaged bearing in a conveyor component, or an abnormal temperature rise could indicate a potential failure in a motor.
Moreover, these sensors also capture condition-based data, documenting the normal range of machine baselines and enabling anomaly detection when equipment deviates from these norms. This level of detailed data acquisition allows for a more nuanced understanding of the performance of machines, including the operational health of conveyor components, pumps and motors.
With the ability to monitor equipment vibrations and capture acoustic emissions, wireless vibration sensors effectively facilitate the failure mode analysis, thereby enabling timely maintenance interventions. The data logging capability of these sensors also provides a historical record of asset performance, further aiding in condition monitoring and predictive maintenance strategy.
Q: Can the data collected from wireless vibration sensors be leveraged for advanced analysis options such as machine learning and AI, thus supporting our predictive maintenance market strategy?
A: Most definitively and this is what Miniotec offers in the solution they deliver.
The data collected from the wireless vibration sensors is utilised for advanced analysis options, including machine learning and AI. Wireless vibration sensors generate a wealth of operational data that, when processed and analysed, can yield significant insights into the condition of mining equipment.
Machine learning algorithms can learn from this sensor data, recognising patterns and correlations that may not be immediately apparent to human operators. For instance, a machine learning model might identify a cyclical pattern of vibration level changes indicating a potential bearing replacement requirement in a critical gearbox.
Furthermore, the solution takes this analysis a step further by not only predicting potential issues but also recommending actions. This approach, known as prescriptive analytics, can suggest the most effective maintenance intervention based on factors like the severity of the problem, the cost of downtime and the availability of replacement parts.
In essence, wireless vibration sensors provide the raw data necessary for these advanced analysis options, supporting the predictive maintenance market strategy and enhancing overall operational efficiency in mining operations.
Q: How can wireless vibration sensors help us in reducing the economic impact of unplanned downtime, and maximising the lifespan of our mining machinery?
A: Wireless vibration sensors can significantly reduce the economic impact of unplanned downtime by providing early warning signs of potential equipment failures. These sensors are specifically designed to measure and monitor vibration levels in industrial machinery, a key indicator of machine health. They can detect changes in vibration patterns that may signal issues such as misalignment, imbalance or bearing wear, often well before these issues lead to machinery failure.
By identifying these issues early, you can schedule maintenance interventions at convenient times, rather than dealing with unexpected breakdowns that halt production. This proactive approach to maintenance, known as predictive maintenance, can result in substantial cost savings. Not only does it reduce the costs associated with emergency repairs and production downtime, but it also helps extend the lifespan of your mining machinery.
Wireless vibration sensors are part of the IIoT technology wave that will continue to transform the mining industry. They allow real-time monitoring of machinery and components, transmitting data to a central system or web platform where it can be analysed for actionable insights. This remote monitoring capability is particularly useful in mining environments where machinery can be located in remote or hard-to-reach places. The sensors are designed for long-term reliability and low power consumption, with features such as user-replaceable batteries and IP68 specifications for resistance to harsh industrial environments.
In addition, these wireless vibration sensors are integrated with other sensor types, such as temperature sensors, acoustic emissions sensors and magnetic flux sensors, to provide a more comprehensive view of machine health. No other wireless vibration sensor on the market has this capability. By continuously monitoring these key measurements, you can gain a deeper understanding of your equipment's performance and can make data-driven decisions that optimise machine longevity and plant efficiency. The fact that these sensors do not required gateways and operate similarly to mobile phones in that they each individually link to the LTE cellular network means that data may start flowing within 10 minutes, putting your mining operations on the fast track to predictive maintenance. This alters everything.
To conclude, the implementation of wireless vibration sensors can be a game-changing strategy for mining operations looking to reduce the economic impact of unplanned downtime and maximise the lifespan of their machinery.
For more Frequently Asked Questions regarding Wireless Vibration Sensors, please read this article.
Let us know your thoughts?
Stay safe.
Best;
About Miniotec:
Miniotec is a digital consulting and technology solutions provider, dedicated to supporting companies in their digital transformation journeys. Established by a group of experienced engineers, we emphasise the harmonious integration of people, processes and technology. Our team has a rich history of working across various sectors, from energy and resources to infrastructure and industry. We are trusted by the world's largest miners, oil and gas giants, utility companies and even budding start-ups and believe in the transformative power of the Industrial Internet of Things (IIoT) and its role in unlocking valuable data insights. Through IIoT, we aim to facilitate better decision-making, enhance operational activities and promote safer work environments. At Miniotec, our goal is to guide and support, ensuring every digital step is a step forward.
WirelessVibrationSensors
MiningIndustry
PredictiveMaintenance
IIoTinMining
MiningSafety
IndustrialAutomation
MiningEfficiency
MachineHealthMonitoring
RemoteMonitoring
DigitalTransformationInMining
DigitalTransformation
IOT
miniotec