The Digital Mine: Transforming the Future of Mining
- Miniotec - Intelligent Solutions
- May 14, 2024
- 13 min read
Updated: Feb 28
Harnessing the Power of Innovation for a Sustainable and Profitable Mining Industry

Key Takeaways:
Digital technologies like automation, data analytics and IoT are driving a revolutionary transformation in the mining industry, improving safety, productivity and sustainability.
The adoption of digital solutions could unlock up to $190 billion in additional value for the mining sector by 2035, through optimised operations, new revenue streams and business models.
Advanced technologies such as autonomous equipment, robotics, wearables, AR/VR and enterprise platforms are augmenting the mining workforce and streamlining operations.
Real-time analytics, predictive maintenance, digital twins and simulation models are enabling smarter decision-making, resource allocation and mine planning.
Overcoming challenges like budget constraints, skills gaps and cultural resistance through collaborative efforts and strategic digital adoption is crucial for realising the full potential of the digital mine.
Introduction - The Digital Disruption in Mining
The mining industry continues to undergo a digital revolution, driven by the rapid advancements in technologies such as automation, data analytics, robotics and the Industrial Internet of Things (IIoT). This digital transformation is reshaping the core processes and information flow that support operations in the mining sector, leading to improved safety, productivity and environmental sustainability.
In recent years, the mining industry has faced numerous challenges, including volatile commodity prices, increasing operational costs and a growing pressure to improve safety and environmental performance.
In response to these challenges, mining companies continue to embrace digital technologies as a means of optimising their operations and gaining a competitive edge.
According to a recent report by one of the Big 4 Global consultants, the adoption of digital technologies in the mining industry, driven by Industry 4.0 strategies, could unlock up to $190 billion (USD) in additional value by 2035. This value will be realised through improvements in productivity, safety and sustainability, as well as the development of new revenue streams and business models, marking a significant milestone in digital innovation.
One of the key drivers of digital transformation in mining is the need to attract and retain a younger, tech-savvy workforce, emphasising the importance of attraction and retention in the era of Mining 4.0. As the industry faces a skills gap due to an ageing workforce and the retirement of experienced professionals, digital technologies are becoming increasingly important for attracting and engaging the next generation of mining professionals, but also, maintaining or increasing productivity with a smaller workforce.
Automation and Operational Hardware Innovation
Autonomous mining equipment, including self-driving trucks, drills and excavators, are becoming more prevalent in the mining industry, enhancing operational efficiency and safety.
One of the most well-known examples of autonomous mining equipment is the Autonomous Haulage System (AHS) developed by a leading manufacturer of construction and mining equipment, which has been deployed at several mines around the world. The AHS uses a fleet of autonomous haul trucks to transport ore from the mine face to the processing plant. The system is equipped with advanced sensors and control systems that allow the trucks to navigate the mine site without the need for a human driver. This not only improves safety by reducing the risk of accidents, but also increases productivity by allowing the trucks to operate 24 hours a day, 7 days a week.

Another example of autonomous mining equipment is from another manufacturer of construction and mining equipment which allows bulldozers to operate autonomously in mining applications. The system uses a combination of GPS, laser and radar technology to guide the dozer as it performs tasks such as clearing overburden and building haul roads.
Autonomous equipment, robotics and digital technologies are transforming mining operations, driving unprecedented gains in efficiency and safety.
In addition to autonomous equipment, mining companies are also investing in robotics, remote-controlled systems and drone technology for hazardous tasks to augment their capabilities. For example, a manufacturer of construction and mining equipment has successfully demonstrated their advanced remotely operated excavators (also known as teleoperated mining excavators) by operating excavators remotely from a booth in Las Vegas, over 500 kilometres away from their location in Arizona, significantly reducing the risk to human operators.
3D printing (also referred to as additive manufacturing) is a different technology that is being used in the mining industry to improve operational efficiency. By enabling the on-site production of custom-built components and spare parts, 3D printing can reduce costs and delivery times and mitigate part obsolescence, while also improving the availability of critical equipment and demonstrating the benefits of digital innovation in field service management.
Digitally-Enabled Workforce
Wearable technologies and smart personal protective equipment (PPE) are playing an increasingly important role in improving worker safety and productivity in the mining industry, thereby augmenting the safety measures in place.
For example, a provider of wireless communication and tracking solutions for underground mines, has developed a smart hard hat that can monitor a worker's vital signs and location in real-time. The smart hard hat is equipped with sensors that measure the worker's heart rate, body temperature and blood oxygen levels. If the sensors detect any abnormalities, the hard hat can alert the worker and their supervisor, allowing for immediate medical attention if needed. The hard hat also includes a GPS tracker that allows the worker's location to be monitored in real-time, improving safety and enabling more efficient rescue operations in the event of an emergency, thereby using digital innovation to improve the safety of workers.
Augmented and virtual reality (AR/VR) applications are also being used in the mining industry for training, remote collaboration and maintenance tasks. For example, a provider of mining equipment simulators has developed a VR training platform that allows miners to practice operating heavy equipment in a safe and controlled environment.
The VR training platform includes realistic simulations of various mining scenarios, such as operating a haul truck in an open-pit mine or a longwall shearer in an underground coal mine. By allowing miners to practice these tasks in a virtual environment, the platform can improve their skills and confidence, while also reducing the risk of accidents during on-the-job training.
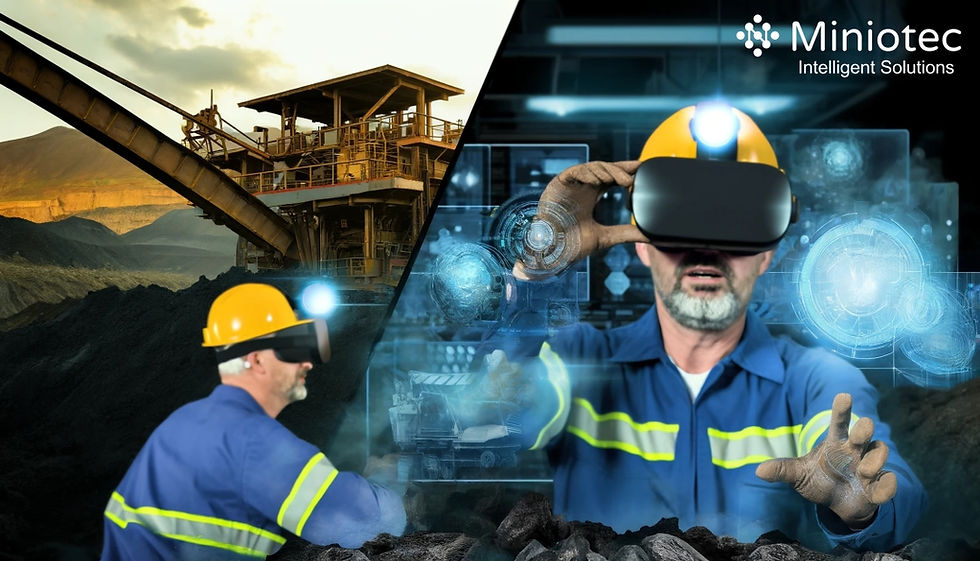
AR applications are also being used in the mining industry. For example, a manufacturer of mining equipment has developed an AR-based remote support system that allows technicians to provide real-time assistance to field personnel. Using AR glasses or a tablet connected through 4G or 5G, field personnel can share their view of the equipment with a remote expert, who can then provide step-by-step instructions for troubleshooting and repair, exemplifying a human-centered approach to technology.
Discover the benefits of advanced conveyor belt monitoring and rip detection to enhance operational efficiency and prevent costly downtime, here.
Integrated Enterprise, Platforms and Ecosystems
Mining companies are investing in enterprise-wide digital platforms to integrate data and processes across the value chain. One example of such a platform provides a comprehensive suite of applications for mine planning, equipment management and production reporting.
The system integrates data from various sources, including GPS, RFID and on-board sensors, to provide real-time visibility into the performance of mining equipment and the progress of mining operations. This information can be used to optimise equipment utilisation, improve maintenance scheduling and identify opportunities for process improvements and optimisation.
In addition to enterprise-wide platforms, mining companies are also forming collaborative partnerships and ecosystems to leverage the expertise of technology providers and drive innovation. For example, one of the world's largest mining companies has established a strategic partnership with Microsoft to accelerate the development and deployment of digital technologies in its operations. Under the partnership, the Tier 1 miner and Microsoft are working together to develop cloud-based solutions for data analytics, artificial intelligence and mixed reality applications. By combining the miner's deep understanding of mining operations with Microsoft's expertise in enterprise software and cloud computing, the partnership aims to create innovative solutions that can drive productivity and sustainability improvements across the mining value chain.
The Importance of Interoperabile Systems
Interoperability between systems and data sources is crucial for realising the full potential of the digital mine. To address this challenge, several industry organisations have developed standards and protocols for data exchange in the mining industry, facilitating a more disruptive and integrated approach to innovation.
For example, the Global Mining Guidelines Group (GMG) supports guidelines and frameworks that promote interoperability in the mining industry. Their work includes consideration of a common framework for integrating data from different systems and applications. This effort is designed to define a set of data models and communication protocols that facilitate the exchange of information between various mining systems, including equipment management, process control and enterprise resource planning (ERP) systems. By fostering interoperability, these guidelines can help mining companies break down data silos, enhance decision-making and drive innovation across the value chain.
Next-Generation Analytics and Decision Support for Digital Mine Solutions
Advanced data analytics, machine learning, computer vision and artificial intelligence are enabling real-time decision-making, predictive maintenance and optimised resource allocation in the mining industry, illustrating the breadth of using digital technologies for efficiency.
One example of a company that is leveraging these technologies is a global mining giant that has developed a centralised data analytics platform called the 'Mine of the Future'. The Mine of the Future platform integrates data from various sources, including sensors on mining equipment, weather stations and satellite imagery, to provide a comprehensive view of mining operations. Using machine learning algorithms, the platform can identify patterns and anomalies in the data, allowing the miner to make more informed decisions about equipment maintenance, production scheduling and resource allocation.
One of the key applications of the Mine of the Future platform is predictive maintenance. By analysing sensor data from mining equipment, the platform can identify potential issues before they occur, allowing maintenance teams to take preventive action and minimise downtime. This not only improves equipment reliability and availability, but also reduces maintenance costs and extends the useful life of mining assets.
Elevate your asset management and optimise your operations: take our online IIoT opportunity evaluation today for actionable insights.
Integrated sensor networks and the Industrial Internet of Things (IIoT) are also playing a critical role in providing mining operations with unprecedented levels of situational awareness and process control. For instance, Miniotec is collaborating with a leading Tier 1 global miner to enhance their operational efficiency through the implementation of IoT Wireless Vibration Sensors on critical mining equipment. This initiative, part of the mining company's broader Digital Transformation strategy, has led to significant cost savings. By analysing the data collected from these sensors (each sensor was installed and delivering data in less than 10 minutes), predictive maintenance (PdM) could be performed more effectively, improving decision making and preventing equipment failures before they happen and thus saving the company hundreds of thousands of dollars within the first year of implementation.

Data-driven technologies are shattering longstanding constraints in mining, enabling smarter, more efficient and sustainable practices.
Another example is from a Tier 2 miner that has deployed a network of sensors and wireless communication systems at its gold mine in Australia to monitor and control various aspects of the mining process. The sensor network includes devices that measure parameters such as ore grade, moisture content and particle size, as well as equipment performance indicators like vibration, temperature and pressure. By integrating this data into a centralised control system, the mine can optimise the performance of the processing plant, improve product quality and reduce energy consumption and waste.
Digital twins and simulation models, enhanced by 5G connectivity, are also being used in the mining industry to optimise mine planning, design and operations in a disruptive fashion. For example, some innovative service companies have developed advanced simulation tools that allow mining companies to create digital replicas of their operations, and in some cases, also test different scenarios before implementing them in the real world. These tools include applications for equipment selection, haul road design and production scheduling. By using these tools to create digital twins of their operations, mining companies can identify bottlenecks, optimise equipment utilisation and develop more efficient mining plans. This not only improves productivity and reduces costs but also helps to minimise the environmental impact of mining activities by optimising the use of resources and reducing waste. For example, Miniotec has equipped a prominent mining firm with fluid condition sensors to monitor and analyse the quality of hydraulic and engine oils in real-time. This technological enhancement allows for predictive maintenance strategies that extend oil change intervals based on actual fluid conditions rather than routine schedules. By leveraging these sensors, the mining company not only ensures optimal machine performance but also significantly reduces waste and operational costs associated with premature fluid changes. This approach not only enhances equipment reliability but also contributes to more sustainable mining practices.
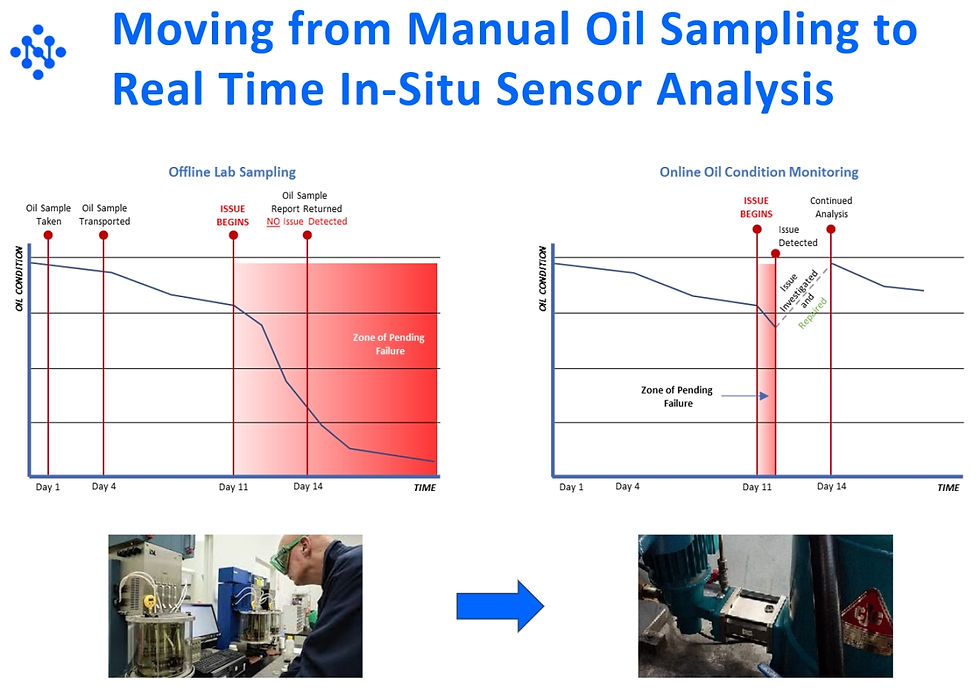
Challenges and Opportunities for Asset Operators
While the largest mining companies have been at the forefront of digital transformation, smaller and mid-tier miners face challenges in adopting these technologies due to budget and resource constraints. According to a mining industry general survey conducted by Miniotec, only 25% of mining companies canvassed have a clear digital strategy and roadmap in place, with the majority of companies still in the early stages of digital adoption.
One of the key challenges facing smaller mining companies is the lack of in-house expertise and resources to implement and maintain digital technologies. Many mining companies lack the IT infrastructure, data management capabilities and technical skills required to effectively deploy and leverage digital solutions. This can lead to costly implementation failures and limited returns on investment (ROI) without a thorough upskilling of the workforce to adapt to the disruptive technologies, emphasising the need for an augment and rethink of workforce training and digital maturity.
Another challenge is the need for cultural change within mining organisations to embrace digital transformation. Many mining professionals are accustomed to traditional ways of working and may be resistant to adopting new technologies and processes. Overcoming this resistance requires strong leadership, effective change management and ongoing training and support for employees to reach new levels of digital innovation maturity.
Despite these challenges, the potential benefits of the digital mine, including improved safety, productivity and sustainability are driving the industry to overcome these barriers and embrace the digital revolution.
According to a report by the World Economic Forum, the adoption of digital technologies in the mining industry could reduce fatalities by up to 80%, increase productivity by up to 30% and reduce greenhouse gas emissions by up to 50%.
To capitalise on these opportunities, mining companies need to take a strategic and holistic approach to digital transformation. This includes developing a clear vision and roadmap for digital adoption, investing in the necessary infrastructure and skills and fostering a culture of innovation and collaboration, with an emphasis on the disruptive potential of technologies like 5G / 6G and cobotics in the mining sector. By working together with technology providers, industry organisations and other stakeholders, mining companies can accelerate the pace of digital transformation and unlock the full potential of the digital mine.
Mining's Next Frontier: Disruptive Technologies on the Horizon
As the mining industry looks to the horizon, a wave of cutting-edge technologies promises to reshape operations in ways once thought unimaginable. From autonomous robotic swarms to the exploitation of biological processes, the next decade could see mining undergo a profound metamorphosis.
Swarm robotics and collective intelligence systems could transform efficiency, with coordinated swarms of small robots collaboratively mapping, exploring and even extracting resources. Biological mining and biomimicry approaches mimic nature, harnessing microorganisms and natural processes to sustainably extract minerals.
Quantum computing and advanced simulations have the potential to unlock unprecedented analytical capabilities, optimising every facet of operations. Nanotechnology and molecular manufacturing could yield ultra-materials and mining techniques at the molecular level.
Even the realm of space mining and asteroid harvesting, once confined to science fiction, may become a reality as space exploration accelerates. And augmented cognition technologies like brain-computer interfaces could seamlessly integrate human and machine capabilities - an extension of super intelligent cobotics.
Additionally, the integration of Large Language Models (LLMs) and Generative AI in mining operations is set to exponentially improve the way data is processed and decisions are made. These technologies can synthesise vast amounts of geological data, operational metrics and environmental reports to generate insights and predictive models with remarkable accuracy. By harnessing the power of LLMs, mining companies can optimise their exploration strategies, improve safety protocols, better train people and enhance regulatory compliance by dynamically generating procedural documents and safety guidelines. This not only increases operational efficiency but also significantly boosts innovation in problem-solving and scenario planning within the sector.
While some ideas may seem far fetched, the relentless evolution of innovation ensures that today's improbable will be tomorrow's cutting-edge. Brace for impact as mining and other industries stand poised to embrace a technological revolution that will transform all industry, including mining, for generations to come.

In Summary - Embracing the Future: A Call to Action
The digital mine will continue to transform the mining industry, delivering tangible benefits across the value chain and positioning the sector for a more sustainable and profitable future. By leveraging advanced technologies such as automation, data analytics, AIoT and the IoT, mining companies can optimise their operations, improve safety and environmental performance and create new revenue streams and business models.
However, realising the full potential of the digital mine will require a concerted effort from all stakeholders, including mining companies, technology providers, industry organisations, investors and governments. This will involve overcoming challenges such as budget constraints, skills gaps and cultural resistance, while also fostering a spirit of innovation and collaboration.
It's time for the mining sector to wholeheartedly embrace the digital revolution. Seize the opportunity to optimise operations, drive sustainability and forge a more profitable future through automation, analytics and technological innovation. Collaborative adoption will be crucial to realising the boundless potential of the digital mine.
As the mining industry continues to evolve and adapt to the demands of the 21st century and beyond, the digital mine will play an increasingly important role in shaping the future of the sector. By embracing digital transformation and harnessing the power of emerging technologies, mining companies can create a more sustainable, efficient and profitable industry that delivers value to shareholders, employees and communities alike.
We welcome your insights and experiences.
Stay safe.
Best;
Special thanks to Tony Nitchov for his expert contributions to this article.
Curious about Wireless Vibration Monitoring? Read our FAQ guide.
About Miniotec:
Miniotec is a digital consulting and technology solutions provider, dedicated to supporting companies in their digital transformation journeys. Established by a group of experienced engineers, we emphasise the harmonious integration of people, processes and technology. Our team has a rich history of working across various sectors, from energy and resources to infrastructure and industry. We are trusted by the world's largest miners, oil and gas giants, utility companies and even budding start-ups and believe in the transformative power of the Industrial Internet of Things (IIoT) and its role in unlocking valuable data insights. Through IIoT, we aim to facilitate better decision-making, enhance operational activities and promote safer work environments. At Miniotec, our goal is to guide and support, ensuring every digital step is a step forward.
Digital Transformation Mining
Mining Industry Innovation
Autonomous Mining Equipment
IoT in Mining
Predictive Maintenance
Digital Twin Mining
Mining Workforce Technology
Sustainable Mining Practices
Mining Safety Technology
Mining Data Analytics
Net Zero Emissions
Sustainable Asset Management
IoT in Asset Management
AI and Predictive Maintenance
Lifecycle Cost Reduction
Predictive Maintenance
Sustainable Asset Lifecycle
Digital Transformation
Industrial IoT
AI in Maintenance
Smart Maintenance
Miniotec