Improving Maintenance Productivity, Even During a Resource Squeeze
- Miniotec - Intelligent Solutions
- Aug 1, 2022
- 4 min read
Updated: Mar 7, 2024
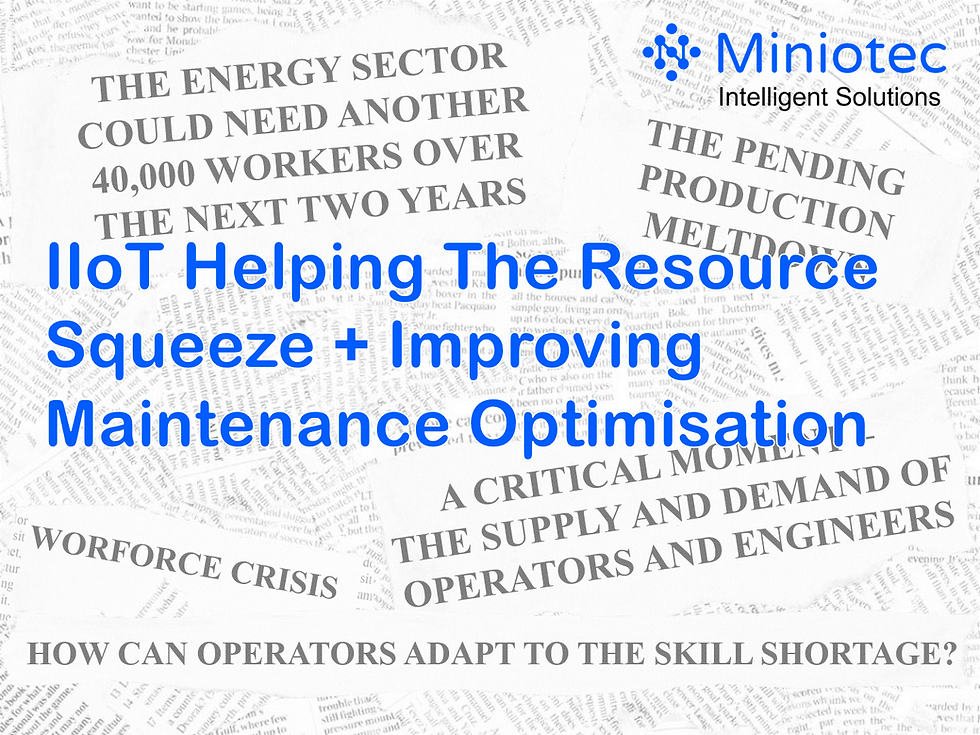
How will a Digital Transformation Strategy with IIoT enable our maintenance teams to be more productive?
How can I improve our maintenance practices when we are unable to find more maintenance personnel?
These are some general questions we have been asked on various occasions from C-suite, Senior Management leaders to Maintenance managers.
The response we offer though can differ depending on the perspective of the person asking the question. The rationale being is that most current maintenance teams are sized based on response to conventional reactive maintenance strategies where the operations team requests or raises maintenance tickets for issues as they arise, like a ‘squeaky wheel’ philosophy. The more frequent operators raise issues and the longer it takes to resolve, Maintenance management have validation to require more maintenance members. In times when maintenance requests are not as prevalent, when cost cutting is required or when maintenance personnel retire or resign, Senior Management leaders may not act or approve budgets to replace them.
Thus the leading question is best not posed to how an IIoT Digital Transformation strategy will make Maintenance teams more productive but "How can IIoT support our Operations by preventing Assets from failing?” The most important role of Maintenance teams on balance is to prevent assets from stopping and interrupting production, so how best can IIoT assist this aim is the approach Miniotec seek to support.
A key maintenance improvement strategy supported by IIoT solutions is to move from reactive maintenance to more proactive and holistic efficient strategies such as Predictive Maintenance that can optimise existing workflows. Examples of this include Wireless Vibration sensors and Oil Sensors which are technologies that can identify the smallest of problems very early in the failure cycle, well before manual processes can typically identify them. Accordingly, this approach of automated monitoring and analytics liberates an existing maintenance team’s available time, enabling additional capacity to perform more proactive and valuable work.
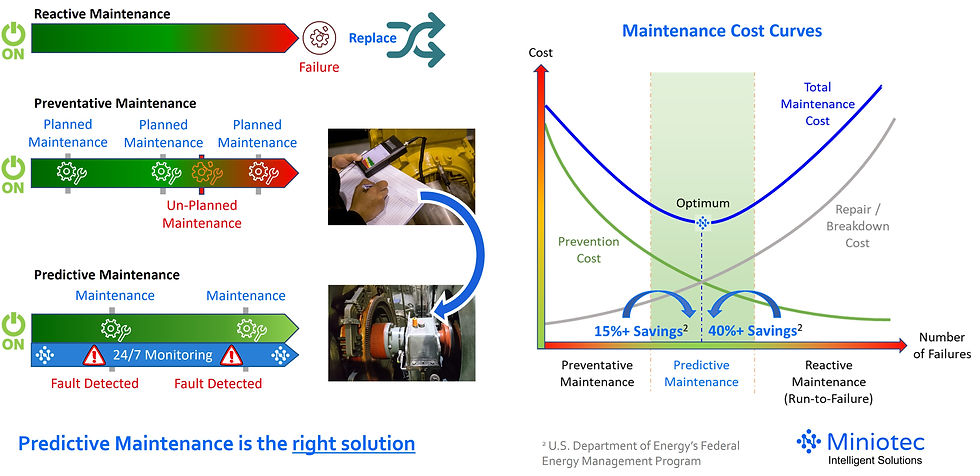
For instance, Client’s have provided examples where Maintenance teams are manually monitoring 50 assets per month through Vibration analysis and taking anywhere between 80-120 hours to collect – analyse – report – act before having to repeat the process. A laborious activity.
Elevate your asset management and optimise your operations: take our online IIoT opportunity evaluation today for actionable insights.
Where IIoT Predictive Maintenance strategies and workflows are embraced, the same collect – analyse – report – act process takes 8-10 hours to complete. A more time efficient process by at least a factor of 10. If you now scale this strategy across your site(s), the benefits multiplied can be immense. How could a maintenance team spend this now additional available time? Most definitely evolving their focus to higher-value tasks as reactive work declines.

Couple this issue of low Maintenance productivity from reactive maintenance strategies with a shortage of available maintenance personnel and the opportunity to improve Maintenance practices becomes unattainable.
IIoT solutions enable asset owners to do more with the same amount of people.
A recent AusIMM report compiled with the inputs from major Energy partners including Rio Tinto, BHP and FMG amongst others, outlined that 87% of these major employers found it ‘difficult’ or ‘very difficult’ to find suitably qualified people to recruit in the last 24 months and almost 90% or these Companies are ‘very concerned’ or ‘concerned’ about having the ability to source suitably qualified personnel in the next 24 months. Unless organisations change there approach to maintenance, where will all the appropriately qualified people come from to improve existing reactive Maintenance strategies?
Recently, the Group of Eight (Go8) universities also released a new policy paper outlining their concerns and plans to address the shortage of a future qualified workforce. According to the paper;
“Australia needs an additional 11,000 engineering enrolments per year over the next five years to meet the government’s projected requirements. This figure takes into consideration dropout rates, workforce retirements and other factors.”
The paper outlines the current shortfall to this enrolment goal is at least 15% but could be as high as 30%.
Which takes us back to a response to the original questions.
For organisations to be able to improve their maintenance productivity and operational performance and/or to improve their maintenance activities despite the shortage of suitably qualified personnel, an IIoT adoption strategy within their Digital Transformation ambitions is essential.

Summary - Improving Maintenance Productivity
Adopting IIoT solutions within a Predictive Maintenance framework enables greater efficiencies and profitability even without altering a current maintenance department team size, all while handling current reactive work events and shifting the Engineer or technician away from routine tasks to more strategic and proactive analysis of data and root cause analysis.
This is because IIoT systems facilitate more data being released, enabling additional value-adding activities that can support improved decision-making for preventing future failures and optimising maintenance tasks.
Organisations should not be complacent with being a good operation. "Move the Needle" with IIoT and make your operations excellent.
Talk to us about how Miniotec can support your operations and provide a step change to your asset management approach in Improving Maintenance Productivity.
For a comprehensive list of Frequently Asked Questions relating to Wireless Vibration Sensors, read this article: https://www.miniotec.com/post/comprehensive-faq-guide-wireless-vibration-sensors
Let us know your thoughts?
We are eager to understand your Digital Maintenance focus and where we could support.
Best;
info@miniotec.com
About Miniotec:
Miniotec is a digital consulting and technology solutions provider, dedicated to supporting companies in their digital transformation journeys. Established by a group of experienced engineers, we emphasise the harmonious integration of people, processes and technology. Our team has a rich history of working across various sectors, from energy and resources to infrastructure and industry. We are trusted by the world's largest miners, oil and gas giants, utility companies and even budding start-ups and believe in the transformative power of the Industrial Internet of Things (IIoT) and its role in unlocking valuable data insights. Through IIoT, we aim to facilitate better decision-making, enhance operational activities and promote safer work environments. At Miniotec, our goal is to guide and support, ensuring every digital step is a step forward.
digitalworker
digitalmaintenance
vibrationanalysis
bigdataandanalytics
futuretrends