Wireless Vibration Sensors: Your Comprehensive FAQ Guide to These Industrial IoT (IIoT) Monitoring Sensors
- Miniotec - Intelligent Solutions
- Aug 13, 2022
- 23 min read
Updated: Oct 25, 2024
Answering Frequently Asked Questions (FAQ) Relating to IIoT Wireless Vibration Sensors to Support Next-Level Condition Monitoring

Introduction to a Vibration Monitoring Sensor System
Welcome to this comprehensive FAQ guide to wireless vibration sensors and their role in the Industrial Internet of Things (IIoT) solutions.
In this article, we will cover everything from the basics of wireless vibration sensors to their applications, benefits and how they can revolutionise predictive maintenance in various industries. We will explore key topics such as remote monitoring, energy efficiency and asset management, focusing on the cutting-edge technology that drives these smart sensors. All of these questions have been directed to Miniotec at various points throughout our Client engagements.
As experts in enhancing operational performance through technology, particularly using IIoT sensors, we understand the importance of staying informed on the latest developments in these solutions which includes wireless vibration sensors. We aim to provide you with valuable insights into the world of predictive maintenance and help you make informed decisions when implementing these transformative solutions.
Full disclosure: Miniotec offers wireless solutions that enhance remote condition monitoring and optimises maintenance, including key features essential for effective performance, such as seamless connectivity and intelligent data analysis to support predictive maintenance strategies. We have a track record of implementing IIoT solutions that support organisations in unlocking the true benefits of digitally transforming the performance of their industrial equipment in their operations and minimising equipment failures. While we offer an innovative wireless vibration monitoring system, this article is designed to provide considered, balanced and far reaching information on wireless vibration sensors and their applications in the industry.
1.) What is a Wireless Vibration Sensor?

A wireless vibration sensor is an Industrial IoT device that measures and monitors vibrations in machinery and equipment without the need for physical connections, such as cables or wires. These sensors typically utilise advanced technologies, such as MEMS or piezoelectric accelerometers, to capture vibration and temperature data. The data is then transmitted wirelessly to a monitoring system or cloud-based platform, where it can be analysed using advanced analytics and artificial intelligence (AI) algorithms. This information is essential for implementing condition-based maintenance (CBM), predictive maintenance and asset performance management (APM) strategies, enhancing operational efficiency, reducing maintenance and asset health management, ultimately improving operational efficiency and reducing downtime.
Elevate your asset management and optimise your operations: take our online IIoT opportunity evaluation today for actionable insights.
2.) How do Wireless Vibration Sensors work and transmit data?
Wireless vibration sensors are easy to install and work by converting mechanical vibrations into electrical signals using an accelerometer sensor. They are a central component to the best condition monitoring systems. The accelerometer measures acceleration, which is then processed through signal processing techniques to monitor vibration, such as RMS velocity, frequency domain and time domain. The sensor typically contains an integrated triaxial accelerometer for capturing vibrations in three orthogonal axes (x, y and z). Wireless communication protocols, such as LTE, Wi-Fi and LoRaWAN, are used for data transfer to a remote monitoring system, IIoT platforms, or cloud-based data analytics solution. Advanced analytics, machine learning and AI algorithms are then applied to the collected data to identify anomalies, predict equipment failures and provide actionable information for maintenance activities.
3.) What distinguishes 'Wired' Vibration Sensors from 'Wireless' Vibration Sensors?

The primary distinction between wired and wireless vibration sensors resides in their connectivity and installation.
A wireless vibration sensor is a device that uses wireless communication systems to transmit data, eliminating the need for physical cables and making installation more straightforward and cost-effective.
In contrast, wired sensors require cabling for data transmission and power supply, increasing the initial cost and complexity of installation. A Wireless system offers greater flexibility in hard-to-reach areas, hazardous location installations and large industrial plants, while wired sensors might be preferred in environments where wireless signal interference is a concern.
4.) What are the Key Features of the Best Wireless Vibration Sensors? Why are Triaxial sensors preferred in Vibration Monitoring?
High-quality wireless vibration sensors typically have the following key features:
High sensitivity and accuracy: These sensors provide real-time data and accurately measure a wide range of vibration frequencies and amplitudes, ensuring precise data collection for condition monitoring and predictive maintenance applications.
Triaxial measurement: By capturing vibrations in three orthogonal axes (x, y and z), these sensors provide comprehensive data on equipment health and performance.
Durable and rugged design: A robust, industrial-grade design ensures durability and reliable performance in harsh environments, such as extreme temperatures, moisture and dust.
Long battery life: Power-efficient designs and energy harvesting technologies help extend battery life, reducing maintenance requirements and overall costs.
Easy configuration and installation: Out-of-the-box dashboards and reporting options
Compatibility: With a variety of IIoT platforms, data analytics tools and predictive maintenance software
Data processing capabilities: Onboard data processing and edge computing capabilities (onboard anomaly detection) can filter and analyse data, reducing the amount of data transmitted and improving overall efficiency.
Cyber Security (or cybersecurity): Secure data transmission and authentication features protect against unauthorised access and data breaches.
Compliance: With industry standards, such as ISO10816 guidelines for vibration monitoring or IECeX and ATEX certification for hazardous area installations
5.) What are the primary types of Wireless Vibration Sensors used for Condition Monitoring?
The primary types of wireless vibration sensors used for condition monitoring include:
Accelerometers: These sensors measure acceleration forces experienced by the sensor, which are then converted to vibration data. They are widely used due to their high sensitivity, broad frequency range and ability to detect both high-frequency and low-frequency vibrations. MEMS accelerometers, in particular, are popular for their small size, low-power consumption and high performance. Piezoelectric accelerometers are known for their higher accuracy but are typically bulkier in size.
Velocity sensors: These sensors directly measure the velocity of vibrating equipment, providing valuable information for condition monitoring and machinery diagnostics. While less common than accelerometers, they are sometimes preferred in specific applications where direct velocity measurement is beneficial. Useful for also monitoring slower-speed rotating equipment, such as fans, blowers and some pumps.
These sensors can be combined with a temperature sensor, ultrasonic sensor or other data sources, providing a comprehensive condition monitoring solution for optimal asset health management.
6.) What are the three (3) Crucial Parameters for Measuring Vibration and how well do Wireless Vibration Sensors do this?
The three (3) crucial parameters for measuring vibration are:
Displacement: The change in position of a vibrating component over time. Wireless vibration sensors, particularly those with high-resolution accelerometers, can accurately measure displacement by integrating the acceleration data twice to obtain displacement values. Displacement measurement focuses on the movement of the vibrating object and is suitable for large, slower-speed equipment.
Velocity: The rate of change of displacement, which provides insight into the severity of vibrations. Velocity measurements are appropriate for overall vibration monitoring and detecting issues like unbalance and misalignment. Wireless vibration sensors can measure velocity by integrating acceleration data once, offering accurate velocity measurements for condition monitoring purposes.
Acceleration: The rate of change of velocity, which helps identify high-frequency vibrations and resonances. Wireless vibration sensors excel in measuring acceleration, as accelerometers are inherently designed to capture this parameter directly. Acceleration measurement is useful for detecting high-frequency vibrations, such as those caused by bearing faults.
The best Wireless vibration sensors offer seamless data aggregation and perform well in measuring these parameters due to their advanced sensing technologies, such as MEMS accelerometers and their ability to capture data in three (3) orthogonal axes. This enables comprehensive and precise vibration monitoring, making them highly suitable for condition monitoring applications.
7.) How can an Organisation ensure they are choosing the right Wireless Vibration Sensor for their Wireless Vibration Sensor System?
To select the most suitable wireless vibration sensor for a specific application, consider the following factors:
Measurement range and sensitivity: Ensure the sensor can accurately measure the expected vibration levels and frequencies for the application. Assess the sensor's sensitivity and dynamic range to confirm its ability to capture relevant data.
Mounting options: Select a sensor with appropriate mounting options for the equipment being monitored, such as adhesive, magnetic, or stud mounting. Proper mounting is essential for obtaining accurate vibration data.
Environmental conditions: Choose a sensor that is durable and can withstand the environmental conditions of the application, such as temperature, humidity and dust. Look for sensors with the highest ingress protection (IP) ratings and temperature ranges.
Wireless communication range: Evaluate the required communication range between the sensor and the data collection system. Ensure the chosen sensor supports the desired range and is compatible with any obstacles or interference in the environment. Note that LoRawan, Zigbee, Bluetooth and Sigfox, for example, typically only transmit small packets of data limiting their ability to support best-practice predictive maintenance strategies.
Battery life and power requirements: Assess the sensor's battery life and power consumption, considering the trade-offs between measurement frequency, data transmission and battery life. Energy harvesting capabilities will minimise maintenance requirements.
Integration and compatibility: Verify that the sensor can be integrated into existing monitoring systems and is compatible with the desired communication protocols and IIoT platforms. API's are key to enable easier data aggregation and integration.
8.) What should be considered when setting up Wireless Vibration Sensors?
When setting up wireless vibration sensors, consider the following factors:
Mounting location: Position the sensor as close as possible to the vibration source, ensuring it is mounted securely and correctly aligned with the vibrating equipment. Avoid areas with excessive structural resonance or noise.
Mounting method: Use appropriate mounting methods, such as stud-mount, adhesive-mount, or magnetic-mount, to ensure proper coupling between the sensor and the equipment. (The order outlined is most preferred to lesser preferred). It is critical that the surface is cleaned and prepared well for sensor fixing.
Wireless signal strength and range: Confirm the sensor's wireless communication range and signal strength, considering any obstacles or interference that may affect data transmission. This is where and why the LTE communication protocol can sometimes provide better outcomes.
Network configuration: Configure the sensor network for optimal data collection and analysis, ensuring seamless communication with the data collection system or IoT platform.
Data management and analysis: Integrate the sensor data with a suitable data management platform or analytics tool for effective condition monitoring and predictive maintenance.
Power management: Adjust the sensor's power settings to balance measurement frequency, data transmission and battery life, taking into account the specific application requirements.
Security: Implement robust security measures to protect the wireless sensor network from unauthorised access and data breaches.
9.) What communication protocols are typically used in Wireless Vibration Sensors and which one is preferred? Why?
Typical communication protocols used in wireless vibration sensors include Zigbee, Wi-Fi, Bluetooth Low Energy (BLE), LTE and Low Power Wide Area Networks (LPWAN) like LoRaWAN, Sigfox, Wireless Mesh and Wirepas.
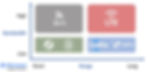
For instance, LTE and Wi-Fi offer higher data rates but consume slightly more power, making them suitable for applications requiring frequent and larger data transmissions.
In contrast, Zigbee, BLE and LPWAN technologies provide generally longer battery life and wider coverage at the expense of lower data rates, making them more appropriate for applications requiring limited data, such as, single point RMS readings.
The preferred communication protocol depends on the specific application requirements, such as range, data throughput, power consumption and condition monitoring strategy. For Predictive Maintenance strategies, full spectral analysis is required which means collecting larger data packets for analytics. For lower speed applications, acoustic data is very important.
For these reasons, we consider LTE provides a good balance between data packet size transmission, excellent penetration through most obstacles and the widest communication coverage. Other protocols, other than Wi-Fi, typically provide threshold alerts, i.e. peak vibration or high temperature.
10.) How do Wireless Vibration Sensors satisfy the primary consideration in Vibration Analysis?
Wireless vibration sensors satisfy the primary consideration in vibration analysis by providing continuous, real-time monitoring of equipment health. This enables early identification of potential issues, which allows for timely corrective actions and maintenance planning. These sensors capture critical vibration data, such as amplitude, frequency and phase, which can be analysed to identify common faults, like imbalance, misalignment and bearing wear. By facilitating the remote monitoring of equipment, wireless sensors reduce the need for manual data collection, improving safety and efficiency while minimising downtime.
11.) What are some downsides to using Wireless Vibration Sensors?
Some downsides to using wireless vibration sensors include:
Limited battery life: Although some sensors have energy harvesting capabilities, most rely on batteries, which require periodic replacement or recharging. Optimising data collection needs and frequency of data collection is thus important.
Signal interference: Wireless communication can be affected by interference from other electronic devices or physical barriers, potentially causing data loss or reduced signal quality.
Network infrastructure requirements: Deployment of wireless sensors may necessitate the installation and maintenance of additional network infrastructure, such as access points or gateways. LTE wireless vibration sensors can often mitigate this constraint.
Security concerns: Wireless networks can be vulnerable to hacking or unauthorised access, so proper security measures must be implemented to protect sensitive data.
Compatibility and integration challenges: Integrating wireless sensors into existing systems or platforms may require additional hardware or software, adding complexity to the implementation process.
Some users cite wireless vibration sensors are more costly than fixed wired sensors. Whilst individual Wireless sensor devices often have a higher upfront cost compared to their wired sensor equivalents, when you include the cost of the installation of wires, cables, potential trenching, cable tray networks etc., wireless vibration sensors are considerably lower over the lifecycle of the asset, but also, provide greater flexibility to install, scale, update or change if necessary.
12.) How does a Wireless Vibration Sensor enable Early Detection of Faults with regards to the Industry Standard P-F curve?
The P-F curve represents the relationship between the point of potential failure (P) and the point of functional failure (F) for a piece of equipment. The curve represents the degradation process, with the goal being to detect faults as early as possible in the timeline.
Wireless vibration sensors enable early detection of faults by continuously monitoring equipment vibration patterns and identifying changes that indicate the onset of failure. By collecting and analysing vibration data in real time, these sensors can detect subtle changes in equipment behaviour that may be indicative of developing issues. This early detection allows for timely intervention and maintenance, effectively extending the period between the point of potential failure and the point of functional failure. As a result, equipment life is prolonged, unplanned downtime is minimised and maintenance costs are reduced.

13.) What are the Major Impacts to Battery Life and Battery Longevity in Wireless Vibration Sensors?
Factors that impact battery life and longevity in wireless vibration sensors include:
Sampling rate: Higher sampling rates consume more power, resulting in reduced battery life. It is essential to balance sampling frequency with battery life for optimal sensor performance.
Transmission frequency: Frequent transmission of data to a remote receiver can drain the battery faster. Strategies like local data storage and processing or adjustable transmission intervals can help conserve power.
Environmental conditions: Extreme temperatures, humidity and other environmental factors can adversely affect battery performance and longevity, potentially necessitating more frequent battery replacements.
Sensor complexity: Advanced sensors with more sophisticated features, such as onboard processing or multiple sensing capabilities, may consume more power than simpler devices.
Power management: Efficient power management algorithms and sleep modes can help extend battery life by reducing power consumption when the sensor is not in active use.
Signal Strength: The weaker the signal the sensor needs to connect to, the harder the sensor has to work and the longer the sensor needs to stay on to transmit the signal. This impacts battery life.
Battery quality: The quality and capacity of the battery itself can influence its overall longevity and performance.
14.) What are the benefits of Online Condition Monitoring compared to Route-Based Monitoring?
The benefits of online condition monitoring through the use of Wireless Vibration Sensors compared to route-based monitoring include:
Continuous data collection: Online monitoring provides real-time insight into equipment health, enabling faster detection of potential issues and more accurate trend analysis.
Improved safety: Remote monitoring reduces the need for technicians to access hazardous or hard-to-reach locations for data collection, enhancing worker safety.
Reduced downtime: Early fault detection allows for proactive maintenance planning, minimising unplanned downtime and associated costs.
More efficient use of Key Resources: Online monitoring reduces the need for manual data collection, allowing technicians to focus on more value-added tasks and enabling more efficient use of labour resources.
Enhanced data accuracy: Automated, continuous data collection minimises the potential for human error or inconsistency associated with route-based monitoring.
Enhanced data analysis: Online monitoring systems often include advanced analytics and visualisation tools, facilitating more accurate fault diagnosis and predictive maintenance.
Scalability: Online monitoring systems can be easily scaled to accommodate additional sensors and equipment as needed.
15.) How does the Communication Range and Signal Strength affect the Performance of Wireless Vibration Sensors?
Communication range and signal strength directly impact the performance of wireless vibration sensors by affecting data transmission quality, reliability and battery longevity. Insufficient range or weak signal strength can lead to data loss, reduced data quality, or delayed transmission, undermining the effectiveness of the monitoring system. Factors influencing communication range and signal strength include:
Physical barriers: Walls, machinery and other obstacles can attenuate wireless signals, reducing range and signal strength.
Distance: Greater distances between the sensor and receiver can weaken the signal and increase the risk of data loss or transmission delays.
Interference: Electronic devices or other wireless networks operating on the same frequency can cause interference, impacting signal quality and range.
Sensor placement: Proper placement of sensors can help optimise signal strength and range by minimising obstructions and reducing the impact of interference.
To ensure optimal performance, it is essential to consider these factors when designing and deploying any wireless vibration sensor.
16.) How do Environmental Factors (Temperature, Humidity, etc.) impact the Performance and Reliability of Wireless Vibration Sensors?
Environmental factors can significantly impact the performance and reliability of wireless vibration sensors.
Temperature extremes can affect sensor accuracy, battery life and electronic components' durability. High humidity or moisture can potentially cause corrosion or short circuits, leading to sensor failure or unreliable data. Dust, dirt and other contaminants may also interfere with the sensor's sensing elements or communication components, reducing data quality and system reliability.
To mitigate these effects, it is essential to choose sensors with appropriate ingress protection (IP) ratings (the higher the rating the better), select components designed for the specific environmental conditions and implement proper maintenance practices.
Not all sensors have high / low temperature tolerances, thus ensure you check this when selecting your preferred wireless vibration solution.
17.) What security and Data Encryption features must be considered in Wireless Vibration Sensors to offer Cyber Security and Protect Sensitive Information?
To ensure cyber security and protect sensitive information in wireless vibration sensors, several security and data encryption features should be considered:
Data encryption: Use of strong encryption protocols, such as Advanced Encryption Standard (AES 128 is good (standard) whereas AES 256 is preferred), for secure data transmission between the sensor and the receiver or gateway.
Access control: Implementing role-based access control (RBAC) to limit system access to authorised personnel.
Authentication: Ensuring secure sensor and receiver authentication mechanisms, such as passwords or digital certificates, to prevent unauthorised devices from connecting to the network.
Secure communication protocols: Utilising secure communication protocols, such as SSL/TLS, can protect data integrity during transmission.
Firmware updates: Regularly updating sensor firmware to address potential vulnerabilities and maintain the highest level of security.
Security monitoring: Implementing intrusion detection systems (IDS) or intrusion prevention systems (IPS) to monitor for and respond to potential cyber threats.
Security audits: Regular security audits can identify vulnerabilities and ensure compliance with industry standards and best practices.
18.) How can Wireless Vibration Sensors be integrated with existing Monitoring Systems or Automation Platforms?

Wireless vibration sensors can be integrated with existing monitoring systems or automation platforms through several methods:
Protocol compatibility: Ensuring that the wireless vibration sensor system supports communication protocols used by the existing monitoring system or automation platform, such as Modbus, OPC-UA, or MQTT.
Application Programming Interfaces (APIs): Leveraging APIs provided by wireless vibration sensor manufacturers or the monitoring system vendor to enable seamless data exchange and integration between the systems. HTTPS is common.
Custom software solutions: Developing custom software solutions to integrate wireless vibration sensor data with existing systems, ensuring the smooth flow of information and enabling comprehensive monitoring and analysis.
Cloud-based platforms: Utilising cloud-based platforms that can aggregate data from various sources, including wireless vibration sensors and existing monitoring systems, for unified data management and analysis.
Gateway devices: Utilising gateway devices that can convert sensor data into a format compatible with the existing system, facilitating data integration and communication.
19.) What are the IP Ratings of the better Wireless Vibration Sensors and how do they ensure Protection against Dust, Water and other Environmental Factors?
The better wireless vibration sensors typically have IP ratings of IP67 or IP68. These ratings ensure protection against dust, water and other environmental factors:
IP66: Provides complete protection against dust ingress and high-pressure water jets from any direction.
IP67: Ensures complete protection against dust ingress and temporary immersion in water up to 1 meter for 30 minutes.
IP68: Guarantees protection against dust ingress and continuous immersion in water beyond 1 meter, as specified by the manufacturer.
By selecting sensors with appropriate IP ratings, end-users can ensure reliable performance in challenging environmental conditions.
20.) What types of Intrinsically Safe Wireless Vibration Sensors are available for Hazardous Environments and which Specific Certifications ensure their Safe Operation in such conditions?
Intrinsically safe wireless vibration sensors are designed for use in hazardous environments where the potential for explosions or fires exists due to the presence of flammable gases, vapours, or dust. These sensors are built to limit the electrical and thermal energy output to prevent ignition of the surrounding atmosphere. Specific certifications for intrinsically safe wireless vibration sensors include:
ATEX (Europe): Ensures the sensor complies with the European Union's directive for equipment intended for use in potentially explosive atmospheres.
IECEx (International): A globally recognised certification provided by the International Electrotechnical Commission for equipment intended for use in explosive atmospheres.
Additionally, other requirements may be required for more niche work zones, e.g. underground mining environments.
When selecting wireless vibration sensors for hazardous environments, it is crucial to choose sensors with the appropriate certifications for the specific location and application. This will help ensure safe operation and compliance with regional regulations.
21.) What are the recommended installation practices for Wireless Vibration Sensors to ensure Optimal Performance and Longevity?
To ensure optimal performance and longevity of wireless vibration sensors, consider the following installation practices:
Surface preparation: Clean and degrease the mounting surface to ensure proper sensor contact and adhesion, reducing the potential for measurement errors.
Mounting method: Properly mount the sensor on a clean, flat surface using appropriate mounting hardware, such as or studs, adhesive or magnets, to ensure a stable and secure connection between the sensor and the monitored equipment.
Orientation: Install the sensor in the appropriate orientation to capture the necessary vibration data from the equipment, taking into account the sensor's sensitivity axes.
Signal quality: Verify the signal quality after installation, ensuring there is a clear and strong communication link between the sensor and the receiver or gateway.
Environmental protection: If needed, use protective covers or enclosures to shield the sensor from extreme environmental conditions, such as high temperatures, corrosive substances, or heavy mechanical impacts, also ensuring suitable ingress protection (IP) ratings.
Periodic inspections: Conduct regular inspections of the sensor and mounting hardware to ensure they remain in good condition, making necessary adjustments or replacements as needed.
22.) How can Wireless Vibration Sensors support the workforce in any industry?
Wireless vibration sensors can positively impact the workforce in various industries by enhancing productivity, safety and decision-making:
Reduced downtime: Timely detection of potential equipment failures allows for proactive maintenance, minimising unexpected downtimes and production losses.
Improved maintenance efficiency: Real-time condition monitoring enables maintenance teams to focus on critical assets, optimising maintenance schedules and a maintenance technician's time.
Enhancing safety: By enabling remote monitoring and early detection of equipment issues, workers can avoid hazardous situations and reduce the risk of accidents.
Boosting productivity: By facilitating predictive maintenance and minimising downtime, workers can focus on more value-added tasks instead of reactive maintenance.
Enabling skill development: By providing workers with a better understanding of machine health and real-time data, they can develop new skills in data analysis, decision-making and problem-solving.
Data-driven decision-making: The data collected from wireless vibration sensors can be analysed to identify trends, enabling informed decisions about equipment operation, maintenance and asset management.
Remote access: Wireless sensors allow for remote monitoring of equipment, reducing the need for physical inspections in hazardous or hard-to-reach areas and increasing worker safety.
23.) How easy is it to replace the battery in Wireless Vibration Sensors and are there any Specific Guidelines to follow during the replacement process?
Replacing the battery in wireless vibration sensors is generally straightforward, but the ease of replacement can vary depending on the sensor design. Some guidelines to follow during the battery replacement process include:
Consult the sensor's documentation / user manual for specific instructions on battery replacement, including the recommended battery type and proper disassembly procedure.
Use appropriate personal protective equipment (PPE) and follow safety precautions. When working in hazardous environments, battery replacement shall be performed by first removing the sensor from the hazardous environment. Only once the sensor is in a safe area should the covering cap exposing the battery be removed.
Power off the sensor before beginning the battery replacement to avoid damage to the sensor or potential harm to the user.
Use the correct battery type recommended for the sensor.
Ensure proper installation of the new battery, paying attention to the correct polarity.
After replacing the battery, confirm that the sensor is functioning correctly and re-establish communication with the monitoring system.
Dispose of the old battery responsibly, following local regulations for battery recycling or disposal.
24.) What Equipment is Best Suited to using Wireless Vibration Sensors?
Wireless vibration sensors are well-suited for various equipment types, particularly in situations where wired solutions are challenging or cost-prohibitive. Some examples of equipment best suited for wireless vibration sensors include:
Rotating machinery: Motors, pumps, fans, gearboxes and other balance-of-plant (BoP) equipment can benefit from continuous vibration monitoring, allowing for early detection of faults and wear.
Remote or hard-to-reach equipment: Assets located in inaccessible or hazardous areas can be effectively monitored with wireless sensors, reducing the need for manual inspections.
Mobile or portable equipment: Equipment that is frequently moved or repositioned can benefit from the flexibility and ease of installation offered by wireless sensors.
Large-scale assets: In facilities with numerous assets spread across a wide area, wireless sensors can simplify and streamline the monitoring process by reducing the need for extensive cabling and infrastructure.
Temporary monitoring: Wireless sensors can be quickly deployed for short-term monitoring of equipment during commissioning, troubleshooting, or performance testing.
Other equipment: Other equipment that requires frequent monitoring, which would benefit from the flexibility and scalability of wireless technology.
A very good article which explores this question in more detail can be read here: https://www.miniotec.com/post/asset-criticality
25.) How do Wireless Vibration Sensors help in data collection and creating a Digital Twin for Predictive Maintenance in the IIoT?
Wireless vibration sensors play a critical role in data collection for creating digital twins in the context of predictive maintenance and IIoT.
They continuously monitor equipment health, capturing vibration data and transmitting it wirelessly to an IIoT platform. This data is then integrated into the digital twin, a virtual representation of the physical asset, which enables real-time monitoring, analysis and prediction of equipment performance.
By incorporating data from wireless vibration sensors, digital twins become more accurate and dynamic, allowing for:
Improved predictive maintenance strategies: Digital twins enable advanced analytics, machine learning and AI algorithms to identify patterns and predict potential equipment failures, facilitating proactive maintenance planning.
Enhanced asset management: The insights gained from digital twins help optimise asset performance, extend equipment lifespan and reduce maintenance costs.
Remote monitoring: Digital twins provide remote access to real-time information on equipment health, enabling operators and maintenance teams to monitor assets from anywhere, improving response times and reducing the need for onsite inspections.
26.) How do Wireless Vibration Sensors enhance Worker Safety?
Wireless vibration sensors contribute to worker safety in several ways:
Early fault detection: By continuously monitoring equipment health, these sensors help identify potential risks before they escalate, reducing the likelihood of accidents and improving overall safety.
Remote monitoring: Wireless sensors enable remote access to equipment health data, minimising the need for manual inspections in hazardous or hard-to-reach areas, thereby reducing the risk of accidents or injuries.
Real-time alerts: Wireless vibration sensors can trigger alerts when abnormal conditions are detected, ensuring that personnel can take prompt action to address potential hazards.
Increased safety through reduced exposure to harmful environments: In industries with hazardous environments, wireless vibration sensors reduce the time workers spend in close proximity to dangerous machinery or substances.
27.) How do Wireless Vibration Sensors help Companies Reduce their Environmental Impact while considering Project Scopes 1, 2 and 3?
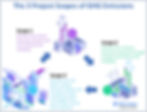
IIoT wireless vibration sensors contribute to reducing a company's environmental impact in several ways, taking into account project scopes 1, 2 and 3:
Improved energy efficiency: By leveraging the power of Industrial Internet of Things (IIoT) and wireless vibration sensors, companies can monitor equipment performance, identify inefficiencies and optimise energy consumption. This results in reduced emissions, a lower carbon footprint and compliance with Scope 1 and 2 greenhouse gas emissions reduction targets.
Resource conservation: Through predictive maintenance and early fault detection enabled by wireless vibration sensors, companies can extend the lifespan of their assets, reducing the need for new equipment production and lowering the consumption of raw materials. This supports a company's Scope 3 environmental goals by minimising the impact of their supply chain on the environment.
Waste reduction: Timely maintenance and proactive asset management, facilitated by advanced analytics and machine learning in wireless vibration monitoring systems, minimise the generation of waste materials, such as worn-out parts or lubricants. This contributes to a cleaner and more sustainable operation, addressing aspects of Scope 3 emissions.
Reduced need for physical inspections: Remote monitoring with IIoT wireless sensors minimises the need for workers to travel to equipment sites for manual inspections, lowering the carbon footprint associated with transportation. This contributes to the reduction of Scope 3 emissions while promoting more efficient and environmentally friendly operations.
By considering all three scopes of emissions and implementing IIoT wireless vibration sensors in their operations, companies can make significant strides towards a more sustainable and eco-friendly future.
28.) What are some of the ways Wireless Vibration Sensors can be used to Improve Energy Efficiency in any Industrial and Manufacturing Environment or Operation?
Wireless vibration sensors can enhance energy efficiency in a manufacturing plant through:
Early detection of inefficiencies: Continuous monitoring of equipment health enables prompt identification of performance issues, such as misalignments, imbalances, or lubrication problems, which can cause increased energy consumption.
Optimised maintenance schedules: Data from wireless sensors facilitates a shift from reactive to proactive maintenance, ensuring optimal equipment performance and reducing energy waste.
Asset performance optimisation: By analysing vibration data, operators can make data-driven decisions to optimise asset performance, increasing overall energy efficiency in the plant.
Downtime reduction: Detecting potential equipment failures before they occur minimises unplanned downtime, allowing for more efficient production processes and reduced energy waste.
29.) How do Wireless Vibration Sensors help in Reducing Maintenance Costs and Increasing Equipment Uptime, leading to a Short ROI?
Wireless vibration sensors contribute to reduced maintenance costs and increased equipment uptime by:
Enabling predictive maintenance: Continuous monitoring of vibration measurement and data analysis allow for the identification of potential issues before they lead to equipment failure, preventing costly reactive maintenance and reducing the risk of unplanned downtime.
Extending asset lifespan: Proactive maintenance based on sensor data helps extend the lifespan of equipment, reducing capital expenditures on new assets.
Reassigning labour costs: Remote monitoring reduces the need for manual inspections, cutting down on labour costs associated with routine equipment checks. With the use of the same available hours, maintenance technicians will now have more time for proactive, 'value add' initiatives that will also include more time available for root cause analysis (RCA) and making other positive improvements to an asset's maintenance management.
Maximising equipment uptime: Early detection of faults enables timely interventions, ensuring that equipment remains operational for a more extended period and improving overall productivity.
30.) How can the data collected from Wireless Vibration Sensors be used to Support ESG reporting and initiatives within an organisation?
The data collected from wireless vibration sensors can support ESG reporting and initiatives by:
Demonstrating energy efficiency improvements: The data enables organisations to track and quantify energy consumption reductions achieved through optimised maintenance and asset performance, supporting their commitment to environmental stewardship.
Promoting resource conservation: By extending asset lifespans and reducing waste generation, wireless vibration sensors contribute to more sustainable operations, helping organisations demonstrate their commitment to responsible resource management.
Enhancing worker safety: The data can be used to showcase efforts in creating a safer working environment, demonstrating social responsibility and commitment to employee wellbeing.
Providing data-driven insights: Accurate and timely data from wireless vibration sensors can be integrated into ESG reports, showcasing an organisation's commitment to data-driven decision-making and transparency in its sustainability initiatives.
In Summary
Wireless vibration sensors are an essential component of the Industrial Internet of Things (IIoT), offering numerous benefits such as improved energy efficiency, remote monitoring and predictive maintenance. These advanced sensors, backed by machine learning and cutting-edge technology, can significantly enhance asset management, reduce downtime and minimise environmental impact across various industries.
By adopting wireless vibration sensors and embracing digital transformation, organisations can unlock their full potential and stay ahead of the competition. We encourage you to explore the world of IIoT solutions, including wireless vibration sensors and consider how they can positively impact your operations. With the right investment in innovative technology and a commitment to continuous improvement, the future of industry is bright and full of opportunities.
Remember to research the available range of wireless sensor options on the market and choose the right solution that best fits your organisation's unique needs and goals.
Please reach out to Miniotec for further guidance; we are committed to supporting your organisation throughout its digital transformation journey. Our approach remains technology-agnostic and we openly share our digital wins and digital scars. We approach each client discussion with the mindset, 'If this were our own time and resources, would we invest in it ourselves? ' With this principle in mind, we prioritise recommending solutions that genuinely align with your operational and financial goals else we won't recommend it.
Let us know your thoughts?
Stay safe.
Best;
About Miniotec:
Miniotec is a digital consulting and technology solutions provider, dedicated to supporting companies in their digital transformation journeys. Established by a group of experienced engineers, we emphasise the harmonious integration of people, processes and technology. Our team has a rich history of working across various sectors, from energy and resources to infrastructure and industry. We are trusted by the world's largest miners, oil and gas giants, utility companies and even budding start-ups and believe in the transformative power of the Industrial Internet of Things (IIoT) and its role in unlocking valuable data insights. Through IIoT, we aim to facilitate better decision-making, enhance operational activities and promote safer work environments. At Miniotec, our goal is to guide and support, ensuring every digital step is a step forward.
Wireless Vibration Sensors
Predictive Maintenance
IIoT
Asset Management
Digital Transformation
Industrial IoT
Smart Monitoring
Machine Health
Remote Monitoring
Condition Monitoring
miniotec
Wireless vibration monitoring systems
Wireless vibration monitoring for industrial use
Wireless vibration sensors for condition monitoring
Real-time wireless vibration monitoring
Wireless vibration monitoring for predictive maintenance
Wireless sensors for industrial equipment
Wireless vibration sensors for manufacturing
Wireless sensor solutions for heavy machinery
Wireless vibration sensors for equipment health
Wireless vibration sensor networks for industrial monitoring
Best wireless sensor networks for condition monitoring
Wireless vibration sensor networks for remote monitoring
IoT-enabled wireless vibration sensor networks
Wireless sensor networks for predictive analytics
Wireless sensors for predictive maintenance
Wireless vibration sensors for asset management
AI-based predictive maintenance with wireless sensors
Wireless sensors for real-time predictive analytics
Predictive maintenance systems with wireless vibration sensors
Advanced wireless vibration sensor technology
Wireless vibration technology for industrial monitoring
Wireless sensor technology for vibration analysis
Wireless monitoring systems for industrial equipment
Wireless monitoring solutions for remote assets
Wireless monitoring for vibration analysis
Wireless condition monitoring for heavy equipment
Wireless vibration monitoring for rotating equipment
Wireless IoT vibration sensors for industrial monitoring
Wireless IoT sensors for vibration analysis
IoT-enabled wireless vibration sensors
IoT-based wireless condition monitoring solutions
Wireless IoT vibration sensors for real-time monitoring
Top wireless vibration monitoring tools
Best wireless tools for vibration analysis
Wireless tools for predictive vibration monitoring
Wireless monitoring tools for industrial maintenance
Wireless vibration tools for real-time monitoring