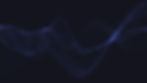
Proactive Conveyor Belt Monitoring: Maximising Conveyor Reliability with AI-Driven Anomaly Detection
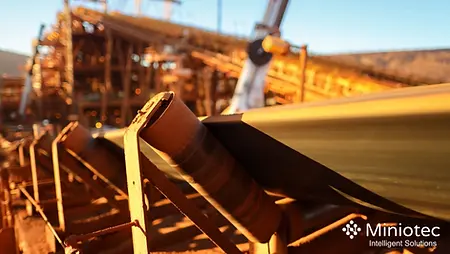
Ensuring the health and functionality of conveyor belts is critical to maintaining their operational efficiency and safety. Unplanned downtime, belt damage and mechanical failures can lead to significant financial losses and productivity disruptions.
Introducing BRaiDS (Belt Rip and AI Damage Detection System) – an advanced industrial
IoT solution designed to transform conveyor belt monitoring, rip detection and maintenance through real-time anomaly identification, predictive maintenance and advanced sensor technology. With BRaiDS, your conveyor belt system will operate more efficiently, reliably and safely.

6 Key Differentiators - Why BRaiDS
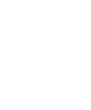
Real-Time Detection & Monitoring
-
Continuous 24/7 Belt Alignment & Tracking
-
Instant Tear, Rip & Misalignment Detection
-
All-In-One Integrated Conveyor Monitoring
-
Near-Instant High-Speed Detection
-
Non-Contact Conveyor Belt Monitoring
-
Load-Point Monitoring for Loaded & Return Belts or any additional location you require

Safety & Risk Mitigation
-
Prevent Catastrophic Belt Failures
-
Early-Detection Technology to Prevent Severe Belt Damage
-
Elevate Health & Safety
-
Unrivalled Stopping Distances
-
No Ionising or other X-ray Radiation

Operational Efficiency & Maintenance
-
Boost Conveyor Productivity
-
Reliability‐Centered Maintenance
-
Minimise Breakdowns & Downtime
-
Mitigate Spillage Cleanup & Costs
-
Achieve Tangible Savings
-
Streamline Shutdown Planning
-
Support Production Targets
-
Versatile Across All Industries
-
Negligible to no Maintenance Required
-
Cost Effective Innovation with High ROI

Installation & Operational Range
-
Rapid Installation (Even on Running Belts where site rules permit)
-
Effective for All Belt Speeds & Widths
-
Compatible with Any Belt Type, Including Steel Core
-
Typically Installed at the Load-Point
-
Handles Any Bulk Material
-
Works with All Product Densities
-
No Structural Modifications Required
-
No Loops, Coils or Belt Alterations
-
No Embedded RFID Tags Needed
-
No Issues with Fibre Cables Breaking

Environmental & Operating Resilience
-
Not Impacted by Dust-Immune; No Lens Cleaning
-
Wide Operating Temperature Range
-
Mud & Caking Resistant
-
Unaffected by Infrared Interference
-
Snow-Proof Design
-
No Enclosure Required
-
Rain-Proof and Weather-Resilient
-
Immune to Direct Sunlight
-
Fog & Misting Resistant
-
No Clean Air Filters Needed
-
No Compressed Air Vessels Needed
-
System has Redundancy should a Sensor Fail

Expertise, Innovation & System Integration
-
Developed from Decades of Mining Experience
-
Proven, Industry-Grade Sensors & Instrumentation
-
Expert Engineering Guidance & Design
-
Edge Analytics for Real-Time Insights (No Cloud Latency)
-
Email & SMS Notifications
-
Programmable Alarm & Trip Conditions
-
Optional Automatic Belt Shutdown
-
We Will Work With You to Integrate Within Your PLC/SCADA Systems
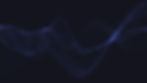
Understanding Conveyor Health and Efficiency: The Role of Proactive Monitoring
" Our advanced conveyor rip detection and protection system, independent of belt brand, retrofits to existing conveyors without troublesome sensor loops or embedded antennae. It supports any speed, product, belt width or length, ensuring reliable, real-time detection and non-destructive condition monitoring to safeguard a conveyor system's longevity and efficiency against operational disruptions. "
BRaiDS offers real-time anomaly detection, allowing for the immediate identification of belt rips, belt misalignment and damage, thereby preventing further belt deterioration. This minimises unplanned downtime and production disruptions, ensuring operational continuity by addressing conveyor issues before they escalate.
The predictive maintenance capabilities of BRaiDS leverage AI and ML algorithms to identify potential failures before they occur. This proactive approach reduces maintenance costs, production losses and extends the lifespan of conveyor belts, supporting digital transformation strategies that seek intelligent mining or smart manufacturing.
In order to consistently verify belt integrity, BRaiDS employs a wide range of different sensor technologies to enable continuous monitoring of belt alignment and condition. It enables the early detection of mechanical issues through vibration and ultrasonic analysis and offers a holistic assessment of operating conditions affecting the belt. Additionally, it detects anomalies through acoustic signature analysis and identifies material accumulation patterns that signify potential system issues.
Ease of implementation is a key feature of BRaiDS. The system is designed for straightforward integration with existing infrastructure, requiring no belt retrofitting and ensuring minimal disruption during installation. This simplifies the installation process, making it accessible for various operational setups.
The system also ensures minimal ongoing maintenance. Durable sensor technology requires minimal user intervention once installed, reducing the resource strain on maintenance teams and allowing them to focus on critical tasks. This guarantees long-term reliability and operational efficiency with minimal oversight.
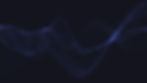
Enhancing Conveyor Belt Operations with Smart Monitoring and Predictive Maintenance
BRaiDS extends the longevity of conveyor components by providing early detection of potential issues such as belt rips, mis-tracking and mechanical failures. This minimises replacement costs and supports advanced condition-based maintenance practices to ensure optimal performance. This significantly enhances overall operational productivity.

It provides continuous operational insights through real-time data analysis, validating belt health while the equipment is still in operation. This helps in understanding the causal relationships between various operational parameters, leading to better decision-making.
The system is designed for scalability and adaptability, accommodating future expansions and technological advancements. It adapts to different operational environments, ensuring broad applicability across industries. By integrating BRaiDS into your conveyor belt system, you are not just adopting a new technology; you are embracing a future of smarter, safer and more efficient conveyor operations.
A High Level Comparison of Traditional Systems and BRaiDS in Conveyor Belt Condition Monitoring